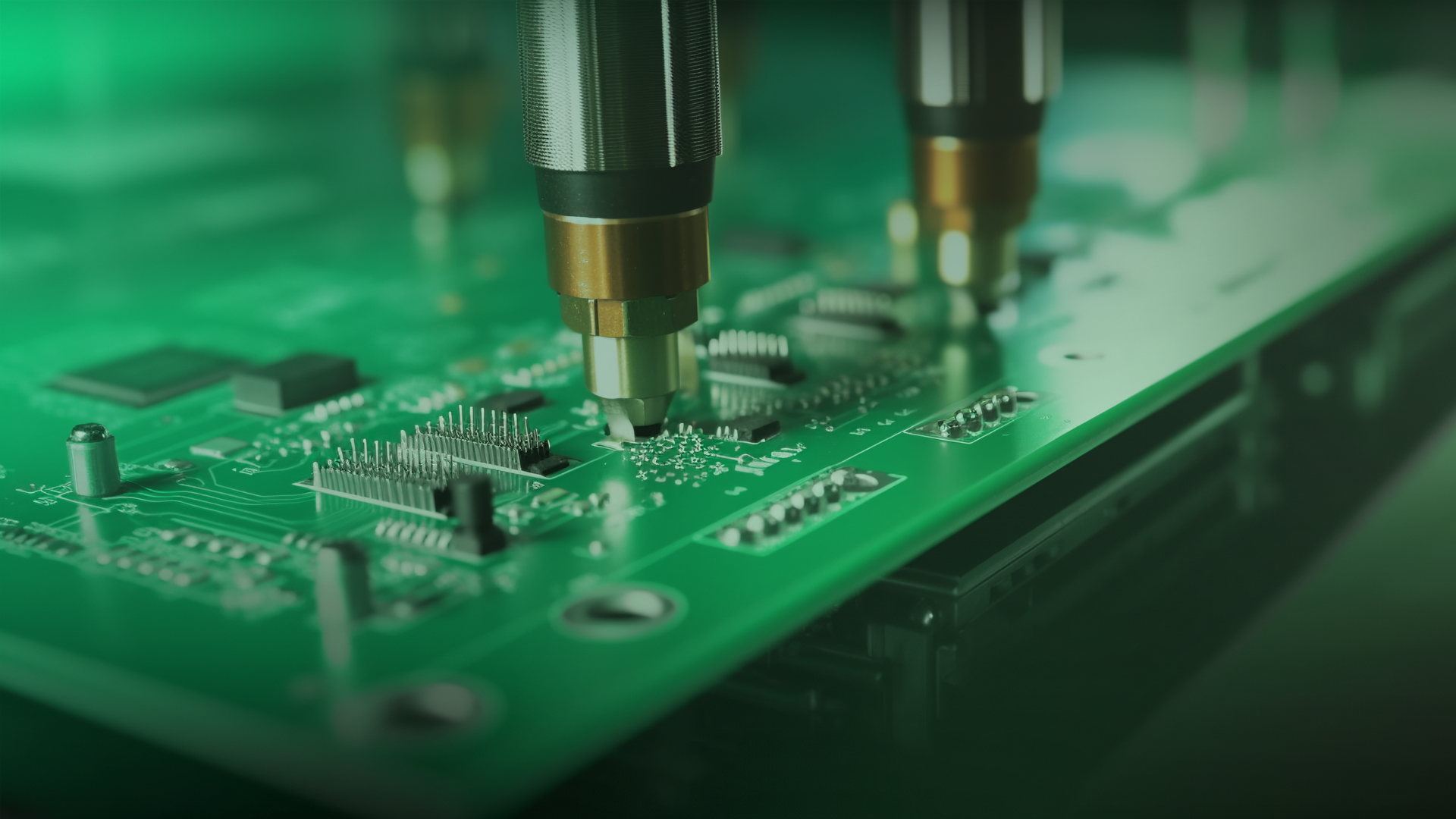
«Постоянная работа над улучшением»: эксперт по внедрению MES — об архитектуре систем управления производством и анализе технологичности
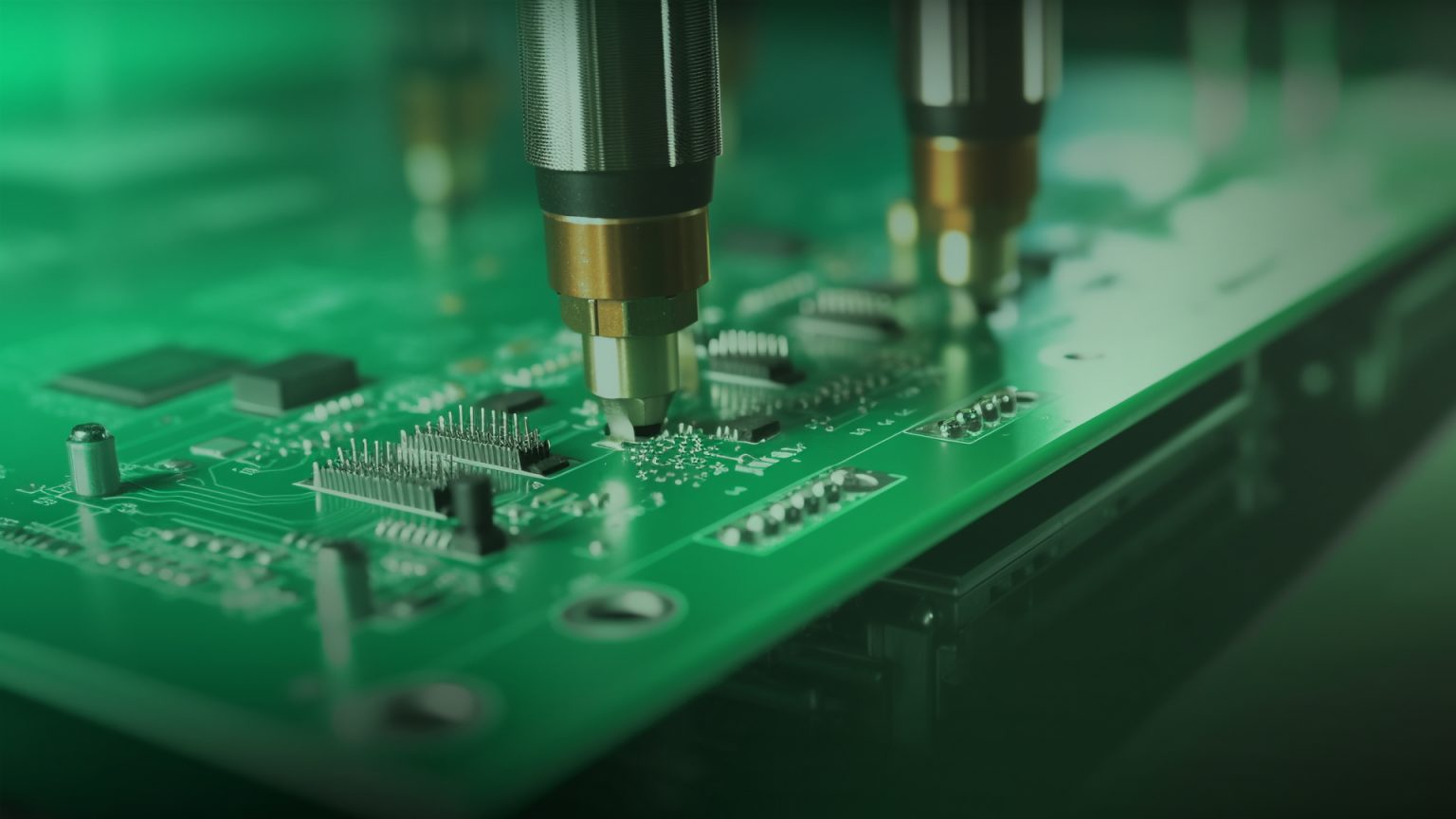
с помощью нейросети
Изготовление печатной платы — длительный и кропотливый процесс, результаты которого на любом этапе может свести на нет технологическая ошибка. Но риск таких ошибок можно значительно снизить при помощи систем анализа технологичности. Об этом Илья Чайковский расскажет в своей лекции.
В беседе с нами Илья пояснил, почему его специальность называется архитектор, какими качествами должен обладать кандидат на эту должность и что станет с его профессией, когда операторов на линии заменят роботы.
- какие предприятия не нуждаются в MES-системах
- в каких ситуациях навыки дипломатии важнее инженерных знаний
- об ошибках, которые лучше не совершать даже по неопытности
MES — это сокращение от manufacturing execution system, то есть система управления производственными процессами. Проще говоря, специальная программа, которая позволяет автоматизировать рутинные, но очень важные операции и собирать, анализировать, а также хранить информацию обо всём, что касается того или иного заказа. С помощью MES можно узнать про плату всё: когда она была изготовлена, на каком оборудовании, по какому заказу и с какими характеристиками.
Тоже в какой-то степени строительством, потому что MES — это, как правило, не одна большая монолитная система. Чаще всего это несколько систем, нередко совершенно разных, от разных вендоров. Моя задача — соединить их между собой в единое целое, создать платформу, которая идеально выполняла бы требования бизнеса.
Их много. И в каждой нише есть свои доминирующие решения. Собственно, в этом разнообразии программного обеспечения и состоит один из главных вызовов моей деятельности, потому что мы очень редко имеем дело с заводом, который строится с нуля. Как правило, MES-системы внедряются на существующем производстве, где уже используется самописное ПО, и с ним тоже надо как-то «дружить». Кроме того, везде разный набор оборудования, алгоритмы подключения в каждом случае свои. Даже два завода, которые производят схожую электронику, работают совершенно по-разному.
На моей практике всегда получалось свести системы к общему знаменателю без написания нового ПО. Современные системы, даже доморощенные, если к их созданию приложили руку компетентные люди, имеют общепринятые интерфейсы обмена информацией и данными. С другой стороны, навыки программирования никогда не будут лишними, потому что индустрия меняется, и одно из веяний — разработка новых продуктов и модулей.
Сомневаюсь. Для работы с MES-системой важно не только знание её самой, но и детальное понимание особенностей конкретного производства. Например, на рынке сейчас сотни единиц разнообразного оборудования и разные поставщики со всего мира. При этом даже если какой-то интегратор продает готовую линию, то её всё равно надо будет достраивать. Возможно даже, что её установят на старом заводе, где параллельно используют оборудование с довоенных времен. Такое бывает, потому что старые станки еще работают, и никто от них отказываться не собирается. Приходится ломать голову, как же их интегрировать в общий производственный процесс. Без опыта участия в реальном проекте это очень сложно. В идеале нужно поучаствовать в таком проекте, где через систему проходит действительно всё производство. К сожалению, в России именно в сфере электроники таких историй крайне мало. Намного чаще встречаешь предприятия, модернизированные не полностью, где оставшаяся часть по-прежнему работает по старинке.
Это общемировой тренд, характерный для многих отраслей, особенно потребительской электроники. Многие потребители хотят обладать уникальным изделием. Но если кому-то достаточно кастомизировать свой смартфон, устанавливая любимую фотографию на экран и настраивая по-своему виджеты, то другому этого уже мало. И в производстве плат такой же тренд. Например, заказчику не нужен Bluetooth-модуль на ноутбуке, но при этом он желает три USB-порта, и чтобы они все были USB 3.0 или Type C. Чтобы сделать всё это, нужна соответствующая плата. Но переделывать плату из-за одного заказчика никто не будет — это слишком трудоемко. Отсюда тренд на бо́льшую вариативность — делают одну плату, которая соответствует разным вариантам.
Прежде чем пустить плату в серию, приходится изготавливать и тестировать опытный образец, чтобы убедиться, что всё работает. Во время этих тестов становится очевидным большинство дефектов. Этот способ верный, но усилия и время он не экономит, так как обнаружение брака вынуждает вносить изменения и повторять заново всю процедуру. Анализ технологичности в электронном виде позволяет избежать таких затрат, выявляя недочёты на цифровом двойнике изделия до производства. Система просчитывает проект и маркирует слабые места, помогая технологу прогнозировать, с какими сложностями может столкнуться производство. Например, система подсказывает, что между компонентами на плате расстояние слишком мало. Технолог проверяет это собственными глазами и уже затем принимает финальное решение: пропустить или согласиться с опасениями машины.
Это естественная процедура, потому что разработчик, который работает над платой, может не знать, как и где она будет производиться, на каком оборудовании, с какими параметрами. Он думает о конструкции — это его первоочередная задача. Но когда конструкторская документация поступает на конкретное предприятие, с ним начинают работу специалисты, цель которых — произвести качественное изделие в срок с минимальными издержками. Они прекрасно знают свою технику и понимают, где можно рискнуть и проверить, а где заведомо будет высокий риск брака.
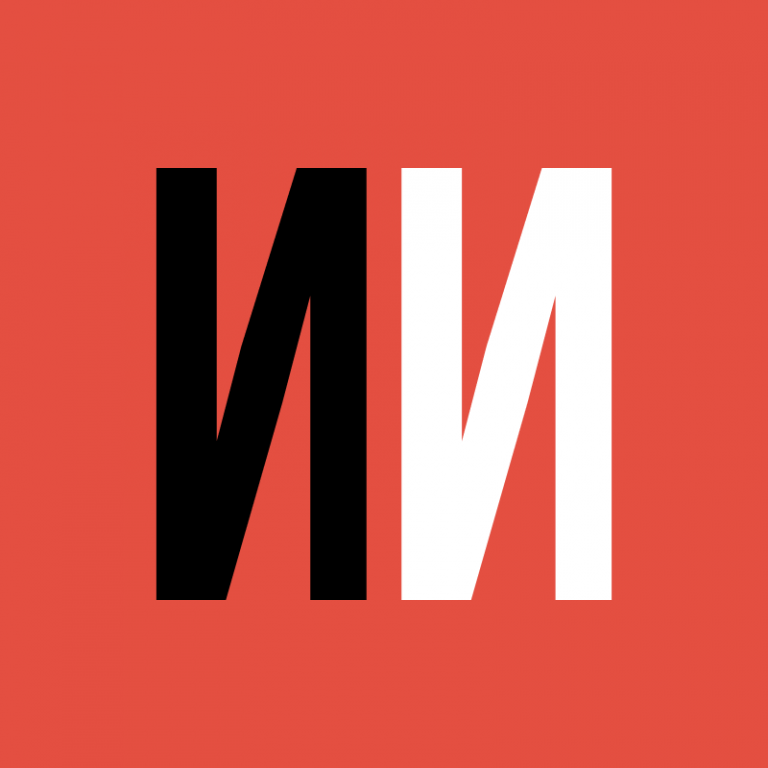
Анализ технологичности монтажа печатной платы: как правильно его проводить и какие нюансы стоит учесть
Я считаю наиболее продвинутой программу Valor Process Preparation от компании Siemens. Есть еще популярный продукт CAM350 от Downstream и ряд систем других вендоров. К тому же анализ технологичности — это лишь один из шагов от конструкции к производству. После него мы берем заготовку, загружаем в оборудование, наносим паяльную пасту, устанавливаем компоненты, перепроверяем, потом в печке всё это спекаем. Когда компоненты поверхностного монтажа установлены, мы несем плату, допустим, на ручной монтаж.
На многих платах есть такие компоненты, которые автоматически устанавливать либо дорого, либо это выходит не очень качественно. Установка самой главной детали — микропроцессора — это тоже, кстати, почти всегда ручная операция.
Прежде всего потребуется голова, потому что придётся много общаться и с инженерами на производстве, и с разработчиками, и с технологами. Со всеми надо поговорить, выяснить, где в работе основные болевые моменты, а где потенциальные точки роста. Всё это необходимо учесть в системе, сбалансировать, протестировать, и уже затем запускать в промышленную эксплуатацию, после чего снова опросить команду и собрать реакцию. Это постоянная работа над улучшением. MES-система в этом смысле — сложный живой организм.
Главное — нужно самому себе четко ответить, зачем всё это делается. Какова конечная цель? Чего нужно достичь в итоге? Очень важно, чтобы ответ на этот вопрос себе совпадал с тем, как это видит руководство компании и руководство производства. Если, например, руководитель производства желает добиться сокращения издержек, повысить оборачиваемость склада, а глава компании думает о том, как перевести учет в цифровую форму и сделать прозрачными все операции, то это разные задачи, и такая разница в понимании будет сильно тормозить весь процесс. В таком случае следует проявить дипломатическую инициативу и попробовать договориться о приоритетах.
Другой важный момент — на раннем этапе поднять вопрос об отношениях с внешней компанией, которая занимается обслуживанием оборудования. Она должна быть готова внести необходимые коррекции в технику. К примеру, мы хотим получать данные о температуре в печи, где происходит припой компонентов. У этой печи свой собственный софт. Соответственно, нужно найти специалиста именно по этому ПО, который выполнит нужные настройки. Как показывает практика, партнеры не всегда охотно на это идут. Особенно если опция внесения корректировок по указанию собственника не была прописана в контракте с обслуживающей компанией.
Пока их можно все пересчитать по пальцам. Но у нас и производств сборки печатных плат, и электроники не так много. Может быть, до десятка крупных. Намного больше предприятий, которые занимаются монтажом компонентов, закупая платы либо в России, либо в Китае.
Это зависит от того, как сильно загружено производство. Если оборудование работает на 30−40% от своего потенциала, то, вероятно, никакая система управления не нужна — всё можно руками сделать. Если номенклатура производимой продукции весьма ограничена — то же самое. Но как только утилизация достигает 60−80% или расширяется ассортимент продукции, сразу возникает потребность в упорядочивании и автоматизации процессов.
На российском рынке многие решения мировых вендоров сейчас перестают быть доступными. С одной стороны, это негативный момент, с другой — такая ситуация стимулирует разработки собственных решений. И что-то мне подсказывает, что в обозримом будущем я стану заниматься такими разработками. Как это пойдет, пока не очень понятно, но уже есть коммерческие частные компании-инвесторы и государственные программы, которые предусматривают в том числе финансирование на разработку ПО. Посмотрим, как это будет реализовываться.
Как показывает мировой опыт эволюции систем управления производством, все они зарождались на каком-то предприятии, где формировалась команда визионеров с предпринимательской жилкой. Эти люди думали не только о том, как автоматизировать свой завод, но и о том, как затем вывести продукт на рынок. Успешные истории заканчивались созданием компании-вендора, которая уже целенаправленно занималась развитием и распространением своей платформы.
Мне кажется, что Россия в этом отношении ничем не хуже, и если у нас сохранится живая конкурентоспособная промышленность, то найдутся и такие первопроходцы. А возможности для развития внутри самой индустрии грандиозны. Отрасли еще только предстоит осваивать различные новые технологии, такие как машинное обучение, компьютерное зрение, дополненная реальность и так далее. Все эти решения могут быть встроены в MES-системы будущего, разработкой которых займутся компании по всему миру. Надеюсь, часть из них окажется с российской пропиской.