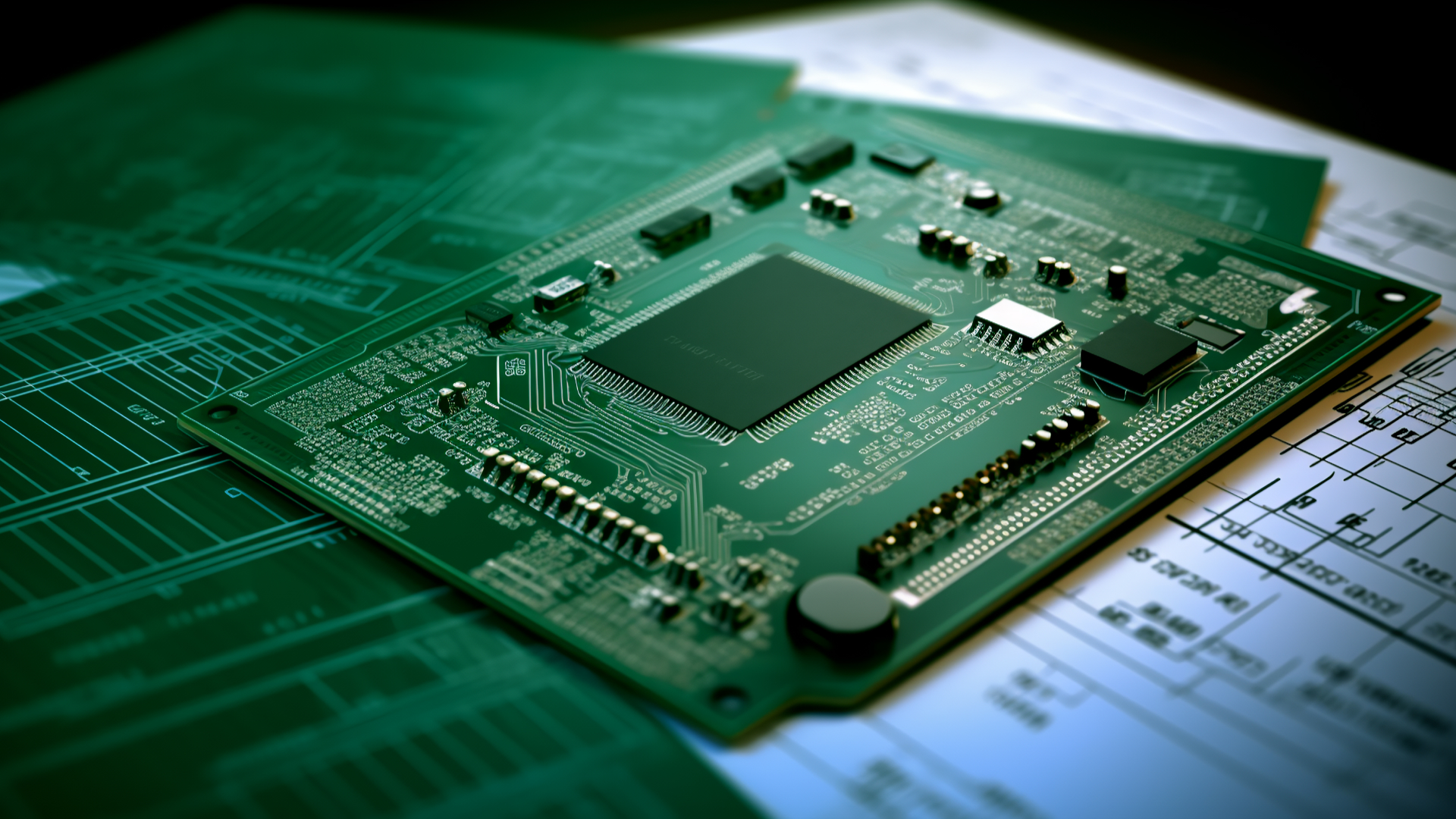
Ключевые характеристики материалов для производства печатных плат
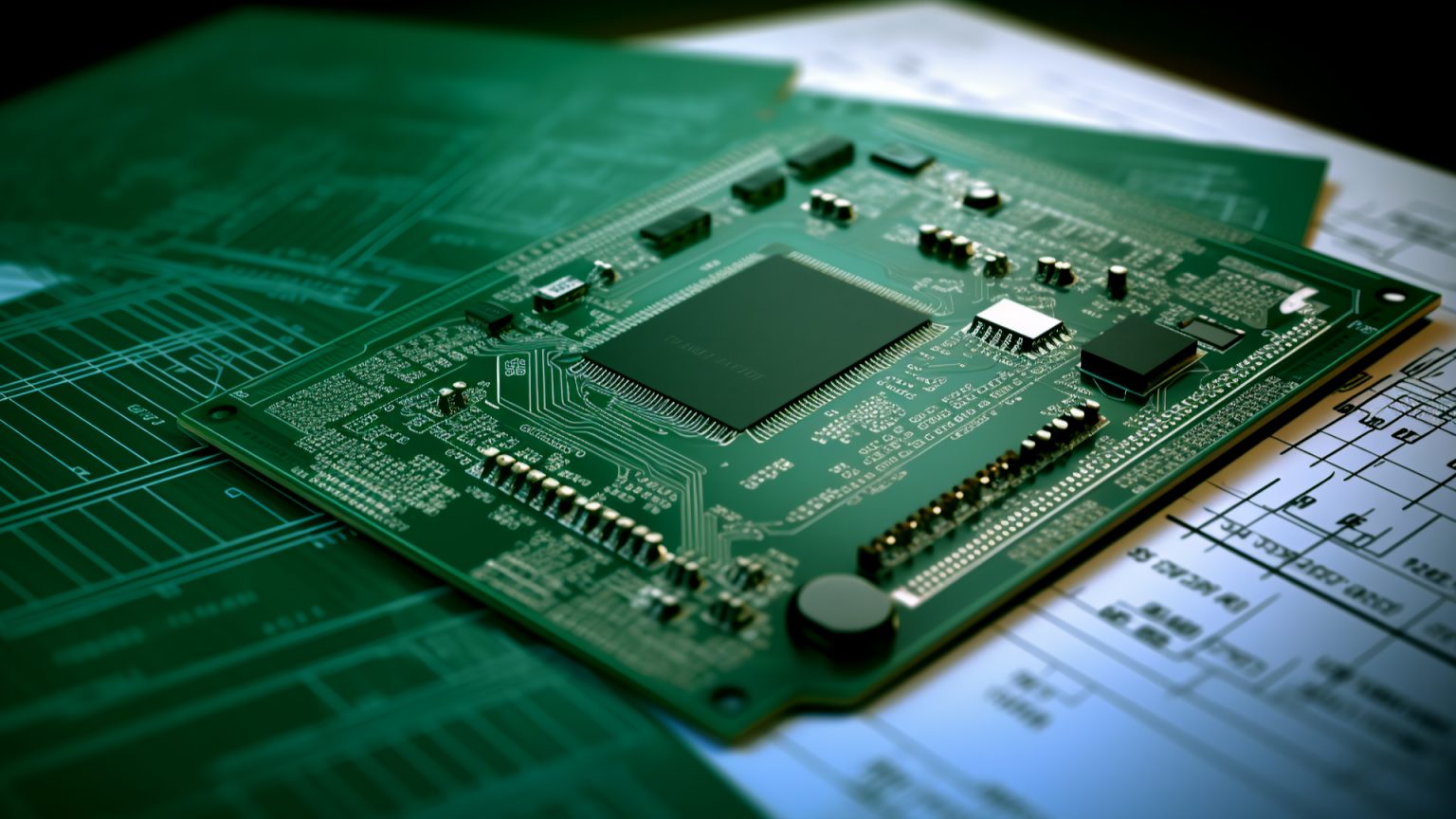
с помощью нейросети
В этой статье мы пройдемся по типовой технической спецификации — документу, в котором собраны требования к базовым материалам для печатной платы: фольгам, препрегам и корам. Поймём, как формируются эти требования. И что важно учитывать, чтобы плата не отправилась в утиль на этапе производства, монтажа или эксплуатации.
Печатная плата — это пластина из диэлектрика, на поверхности и внутри которой сформированы токопроводящие цепи из медной фольги. Фольга может поставляться как отдельными рулонами и листами, так и сразу спрессованной с диэлектриком (тогда это будет уже базовый материал — кор).
Чтобы соединить соседние токопроводящие слои, нужен препрег — лист тканого стекловолокна, пропитанного не до конца отвержденным полимером.
Слой или несколько слоев препрега, покрытый фольгой с двух (реже — с одной) сторон и прошедший полимеризацию, формируют кор, или ядро. На корах обычно реализуют все внутренние слои платы.
Каждый из материалов поставляется в десятках видов и марок, которые отличаются базовыми характеристиками. Давайте посмотрим, как эти параметры влияют на процессы производства.
Основной параметр фольги — шероховатость
С одной стороны, чем выше шероховатость, тем лучше её адгезия в процессе прессования. С другой — с увеличением шероховатости возрастают и потери высокоскоростных сигналов.
Получить отлично спрессованное, но абсолютно нерабочее из-за искажения сигналов изделие не хочет никто. Для решения этой проблемы часто используют коры с RTF-фольгой. Они прессуются на препрег стороной с минимальной шероховатостью.
Так получается кор, в котором фольги гладкой стороной «смотрят» друг на друга. Это даёт хорошие показатели целостности сигнала. При этом RTF-фольга обращена наружу стороной с большей шероховатостью, что обеспечивает лучшую адгезию при прессовании всей платы.
Рекомендации по шероховатости фольги выдаёт инженер по целостности сигнала.
Но базовый принцип прост: чем выше частота сигналов, идущих по плате, тем меньшая шероховатость (в идеале, с обеих сторон) нам нужна.
- HPF (high-performance foil) — 10 μm <Rz <15μm
- STD (standard foil) — 5 μm <Rz <10μm
- VLP (very-low profile foil) — 3μm <Rz <6μm
- RTF (reverse-treatment foil) — 3 μm <Rz <6μm
- HVLP (hyper-very-low profile foil) — 1μm <Rz <3μm
- ULP (ultra-low roughness foil) — 0.5 μm <Rz <1 μm
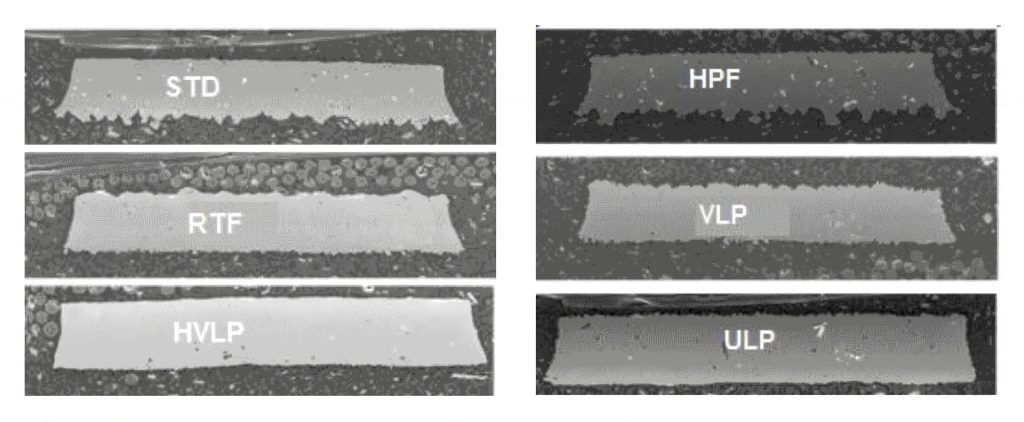
Допуск по этому параметру (Rz) рассчитывается по следующей формуле и методу:
Мы берём образец фольги и профилометром находим 10 точек: 5 наибольших выступов и 5 наибольших впадин профиля в пределах базовой длины. Затем считаем сумму средних абсолютных значений их высот.
Пример профиля фольги с замерами, взятыми на образце длиною в 125 микрон:
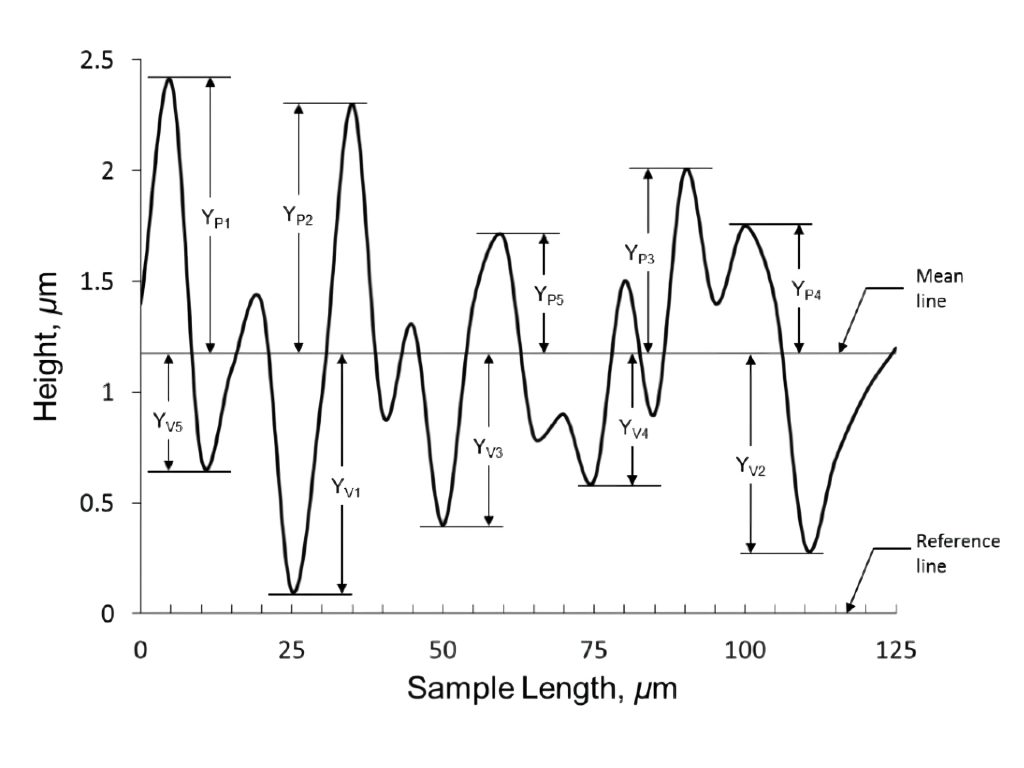
Ключевые параметры для кóров и препрегов
Для этих материалов технические спецификации, как правило, указывают гораздо больше информации. Ниже мы разберём некоторые из них, как они формируются и на что влияют.
Пример вырезок из технической спецификации материалов для производства печатной платы TU-883:
Обратите внимание, что часть характеристик указаны чётко, с конкретными параметрами, а часть — например, CAF-resistance — просто упоминается.
Тип плетения
Напомню, что препреги обычно делаются из плетеного стекловолокна. С одной стороны, варианты с неплотным плетением содержат в себе много смолы, что может упростить заполнение вытравленной меди.
Типы различных плетений в порядке уплотнения:
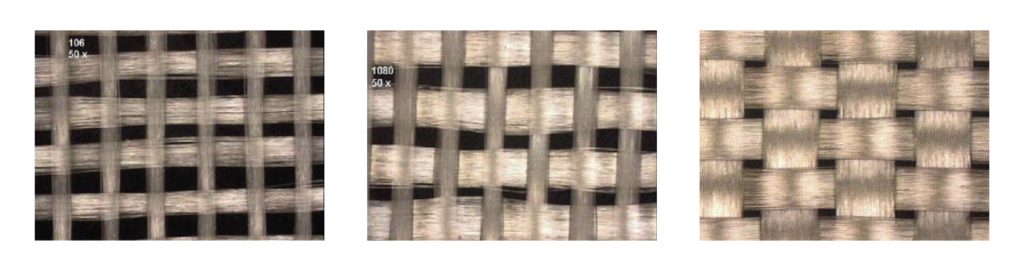
У стекловолокна и смолы разные диэлектрические постоянные (Dk) — следовательно, линии, идущие поверх стекловолокна и смолы, будут иметь разный импеданс и разную скорость распространения сигнала. Такая несогласованность линий диффпары приведёт к ухудшению сигнала.
Для низкочастотной техники неплотное плетение не критично. В остальных случаях, если нет доступа к материалам с более плотным плетением, можно решить проблему другими способами.
Например, расположить плату на производственной панели под углом 15−20⁰. Или вести диффпары под углами 11−13⁰. При таком подходе каждая линия будет идти как поверх стекла, так и поверх смолы, — и особой разницы в импедансах и скорости распространения сигнала между линиями не будет.
По запросу производитель может предоставить более подробную информацию о плетении препрегов. Ниже на примере Isola разберем размеры плетения.
Производитель препрегов предоставляет вот такую таблицу:

В ней для запрашиваемых типов плетения (Glass_type) указаны шаги плетения по Ox (X3_pitch) и Oy (Y3_pitch) и габариты жгутов (шлейфов) стекловолокна, плетёных вдоль этих же осей.
Ширины жгутов обозначены как X2 и Y2.
Шаги плетения — как X3 и Y3.
X1 и Y1 — это толщины жгутов.
Данная информация позволяет получить более детализированное представление о плетении конкретных препрегов, в частности, о зазорах между параллельными жгутами вдоль каждой оси.
Температура стеклования (Tg) и температурные коэффициенты расширения CTEz, CTExy
Температура стеклования — температура, при превышении которой материал переходит из твердого в вязкотекучее состояние. Препрег состоит из стекловолокна, пропитанного не до конца отвержденным полимером (смолой). Собственно, температура стеклования этого полимера нас и интересует. Для печатных плат с шестью и более слоями используют материалы с Tg от 170⁰С и выше.
Чтобы измерить этот параметр, обычно применяют дилатометрические методы измерения, то есть с небольшого кусочка кора предварительно стравливают всю медь, затем пару часов просушивают образец оставшегося диэлектрического материала при температуре около 105⁰С, а после остужают до 23⁰С. После этого образец начинают греть до 250−260⁰С — пиковой температуры в процессе пайки.
Чем более высокотемпературный припой используется при монтаже, тем меньший CTEz нам нужен.
Tg встречается еще в одном месте технической спецификации — как условие измерения CTEz, коэффициента температурного расширения по оси Оz. Этот параметр показывает, насколько будет увеличиваться плата в процессе пайки или другого сильного нагрева, причём с учётом её анизотропной структуры.
Важно, чтобы расширение платы при нагреве также компенсировалось достаточной пластичностью осажденной меди в переходных и монтажных отверстиях. Иначе можно получить разрыв «стакана» отверстия — то есть разрыв целостности электрической цепи, что фатально для любой печатной платы.
Температурные коэффициенты расширения рассчитывают до и после достижения Tg, в технической спецификации они указываются как pre- и post-Tg, соответственно. Некоторые производители также указывают CTE для температурного интервала, соответствующего термопрофилю SMT монтажа (пайки):
Разные типы CTE рассчитывают по своим формулам:
- Расширение материала при нагреве до уровня Tg:
- Расширение материала при нагреве выше уровня Tg:
- Расширение материала при нагреве от комнатной температуры до пика пайки:
- Относительное расширение материала в диапазоне пайки,
где t0 — толщина образца при 23⁰С, измеренная до начала нагрева. Для удобства можно принять t0= tА:
Помимо CTEz учитывается температурный коэффициент расширения в плоскости xOy —CTExy. Он частично отражает, насколько могут изменяться масштабы слоев в процессе прессования платы. Влияние данного фактора можно корректировать перед производством в САМ-программах: слои можно вывести в различных масштабах, например, 1:1,02 или 1:0,97.
Температура разложения (Td)
Тd — температура, при которой материал теряет более 5% своего веса и после остужения разрушается. Выбор материала по данному параметру сильно зависит от используемых в процессе монтажа припоев. Чем выше температура плавления припоя, тем выше должно быть значение Td и Tg. И это один из примеров, почему процесс производства и монтажа платы стоит рассматривать комплексно.
Для плат, монтируемых по бессвинцовой технологии, рекомендуется выбирать материалы с большим значением Td и Tg. Для высокотемпературных припоев — ещё большим.
Большинство современных материалов имеют в технических спецификациях пункт Pb-free compatible — они совместимы с бессвинцовой технологией монтажа и имеют заведомо высокие показатели Td и Tg.
Стоит выбирать материалы с Td, превосходящим пиковую температуру пайки минимум на 100⁰С, а лучше на 150⁰С.
Процент содержания смолы (RC%)
Одни и те же типы плетений могут иметь разные параметры диэлектрической постоянной (Dk) — этот показатель важен для расчета импедансов, о нём я расскажу позже. Разница Dk для одинаковых плетений зависит от количества смолы в них (RC%).
Например, в таблице ниже приведены препреги для платы TU-883. Для типа плетения 1080 есть два варианта содержания смолы: RC63% и RC67%. Толщина второго больше как раз из-за дополнительного количества смолы. И Dk меньше у препрега с большим количеством смолы.
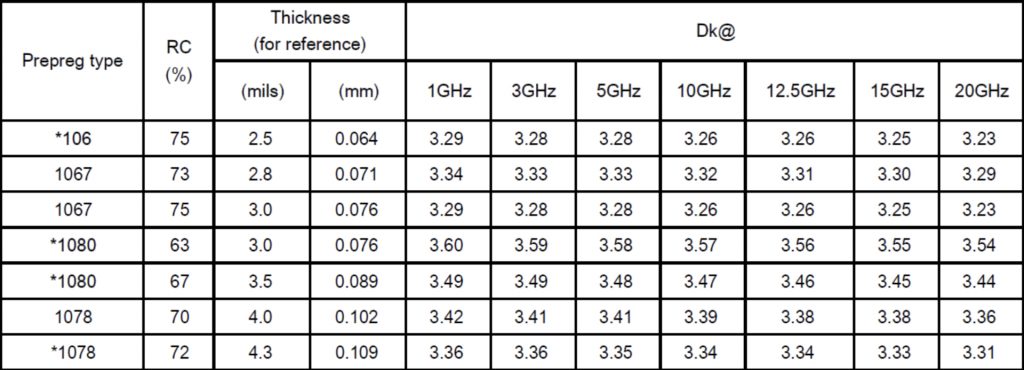
Вывод: чем выше RC%, тем ниже Dk.
Isola, один из поставщиков базовых материалов, для производства плат, рассчитывает Dk препрегов по следующей формуле:
Также важно понимать, что на заполнение вытравленной меди внутренних слоев расходуется только смола, а не стекловолокно. Поэтому при выборе препрегов для прессования необходимо убедиться в том, что смолы в них хватит для заполнения зазоров.
CAF-resistance (сопротивляемость CAF-эффекту)
Conductive Anodic Filamentation (CAF) — эффект миграции ионов меди вдоль трещин/расслоений стекловолокна под действием разности потенциалов. При разности потенциалов проводящие нити могут расти между отверстиями, падами и площадками поверхностного монтажа.
Рис.1: Схематичные изображения CAF-эффекта: прорастание нити от отверстия к отверстию, от пада к отверстию, от пада к паду и от линии к линии
Рис. 2: так проводящие медные нити, прорастающие от одного отверстия к другому в результате CAF-эффекта, выглядят в реальности.
Сопротивляемость CAF-эффекту оценивают с помощью открыть в новой вкладке ->" data-bs-toggle="tooltip" href="javascript:void (0);" data-timage="" data-timageurl="" data-tlink="https://www.ipc.org/caf-test-vehicle-artworks-within-tm-650″ data-theader="ССЫЛКА" data-tsubheading="Gerber-файлы для тест-купонов" data-tdescription="Можно скачать и изучить по ссылке" data-extra-class="--big-tooltip heading-tooltip-show" class="text-tooltip">специальных тест-купонов. Это десятислойные печатные платы с матрицами металлизированных отверстий, подключенными к разным цепям. Купоны, сделанные по стандартам IPC-9255 и IPC-9256, подходят только для оценки CAF-resistance между металлизированными отверстиями (PTH), по стандартам IPC-9253 и IPC-9254 — более расширенные (например могут тестировать PTH to shape — зазору между полигоном и стаканом PTH).
Фрагмент тест-купона по современному стандарту IPC-9256:
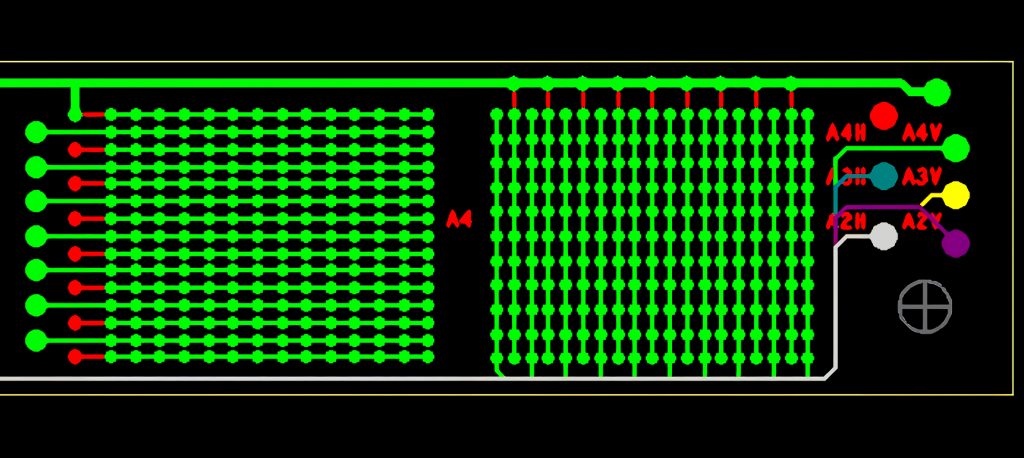
Он, как и IPC-9255, меньше своих предшественников (IPC-9254 и IPC-9253), поэтому его можно размещать по периметру заготовки для более детальной оценки производственного процесса и материала.
Образец проходит симуляцию монтажа и ремонта. Вот примеры симуляции нескольких циклов монтажа с разными температурами припоя:
- Bake (specify), 3X @ 260⁰С Preconditioning (specify profile)
- Bake (specify), 6X @ 260⁰С Preconditioning (specify profile)
- Bake (specify), 6X @ 230⁰С Preconditioning (specify profile)
- Bake (specify), 5X @ 245⁰С Preconditioning (specify profile)
Образцы также проходят симуляцию отмывки. К ним припаиваются провода, через которые впоследствии будет подано напряжение, точки пайки отмываются и образцы сушатся. Далее образец помещается в специальную камеру с изменяемой влажностью и температурой, создается разность потенциалов.
Примеры CAF-тестирования параметров — напряжения, температуры, влажности — в рамках Temperature Humidity Bias Test:
- 15 Vdc, 50⁰С, 80% RH,
- 100 Vdc, 65⁰С, 87% RH,
- 10 Vdc, 65⁰С, 85 $ RH.
После платы стабилизируются и замеряется сопротивление изоляции. Платы со значительным падением сопротивления изоляции бракуются.
Влагопоглощение (moisture/water absorption)
Любой материал набирает влагу, коры и препреги — не исключение. С увеличением показателя влагопоглощения снижается реальная Td и CAF-resistance.
Если насыщенную влагой плату пропустить через печь оплавления, из-за слишком быстрого выхода влаги она может просто расслоиться. И даже если непросушенная плата выдержала печь, мы можем получить увеличенное коробление после пайки, превышающее допустимые стандартные значения.
Так выглядит индикатор влажности внутри упаковки, в которой платы прибывают на участок монтажа:
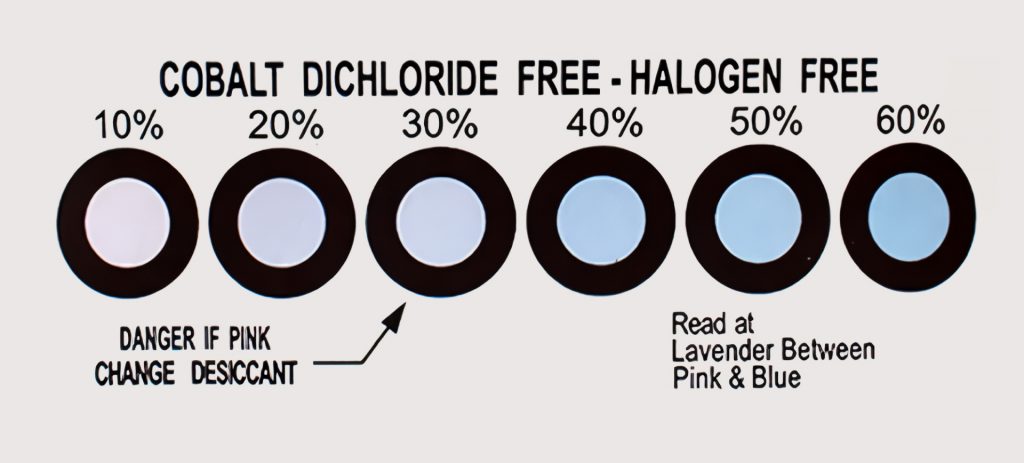
После изготовления на заводе платы упаковываются и отправляются на участок монтажа. Если при вскрытии упаковки индикатор влажности зашкаливает, платы дополнительно просушивают в специальном шкафу перед монтажом.
Если печатный узел должен будет работать во влажной и соленой морской среде, стоит уделить особое внимание подбору материала с низким влагопоглощением и высоким сопротивлением CAF.
Иначе он с высокой вероятностью выйдет из строя еще до конца гарантийного срока.
Иногда в технических спецификациях указывают обратный параметр — moisture/water absorption resistance. То есть защита от влаги. Тогда наоборот: чем он больше, тем лучше.
Диэлектрическая постоянная (Dk) и тангенс угла диэлектрических потерь (Df)
Эти параметры важны для расчета импедансов различных топологий и потерь сигналов. В некоторых случаях приходится заменять материалы для производства платы. И тогда необходимо убедиться, что заменяющий материал имеет схожий Dk и Df не больше, чем у оригинального материала. В большинстве случаев удаётся подобрать Dk достаточно близкий, чтобы с учетом техпроцесса остаться в стандартном допуске на импедансы +/-10%
Производство может само пересчитать импедансы, но тогда оно должно отправить их в RnD на согласование. Либо может попросить RnD внести правки в проект с учетом измененного Dk.
Как верно подобрать материалы
Большинства проблем можно избежать, если заранее согласовать ваш выбор с технологиями завода и их типовыми материалами. Отличной практикой будет получить производственный стек от фабрики перед размещением заказа: возможно, вам предложат препреги с большим RC, что позволит заполнить все зазоры на внутренних слоях. А вы сможете убедиться, что соблюдены ваши требования к расстояниям между сигнальных слоев и от сигнальных линий до их опор, ведь заводской стек будет рассчитан с учетом усадок препрега, расходуемого на заполнение зазоров топологии.
Вы также можете заранее уточнить у завода базовую шероховатость фольги и до какого Rz она развивается на каждом этапе от нанесения фоторезиста до подготовки слоев к прессованию. С повышением частот сигналов шероховатость поверхности становится так же важна, как и Df материала, иначе вам грозят потери сигналов, из-за которых плата не заработает на нужных частотах.
Если же в штате разработчиков нет человека, хорошо знакомого с характеристиками материалов и технологией производства плат, стоит регулярно консультироваться с технологами заводов, на которых будет производиться плата. Они помогут подобрать материал с подходящими для вашей технологии монтажа Tg, Td и другими нужными параметрами.
Отличный материал, спасибо! Еще несколько тем стали прозрачны/понятны.