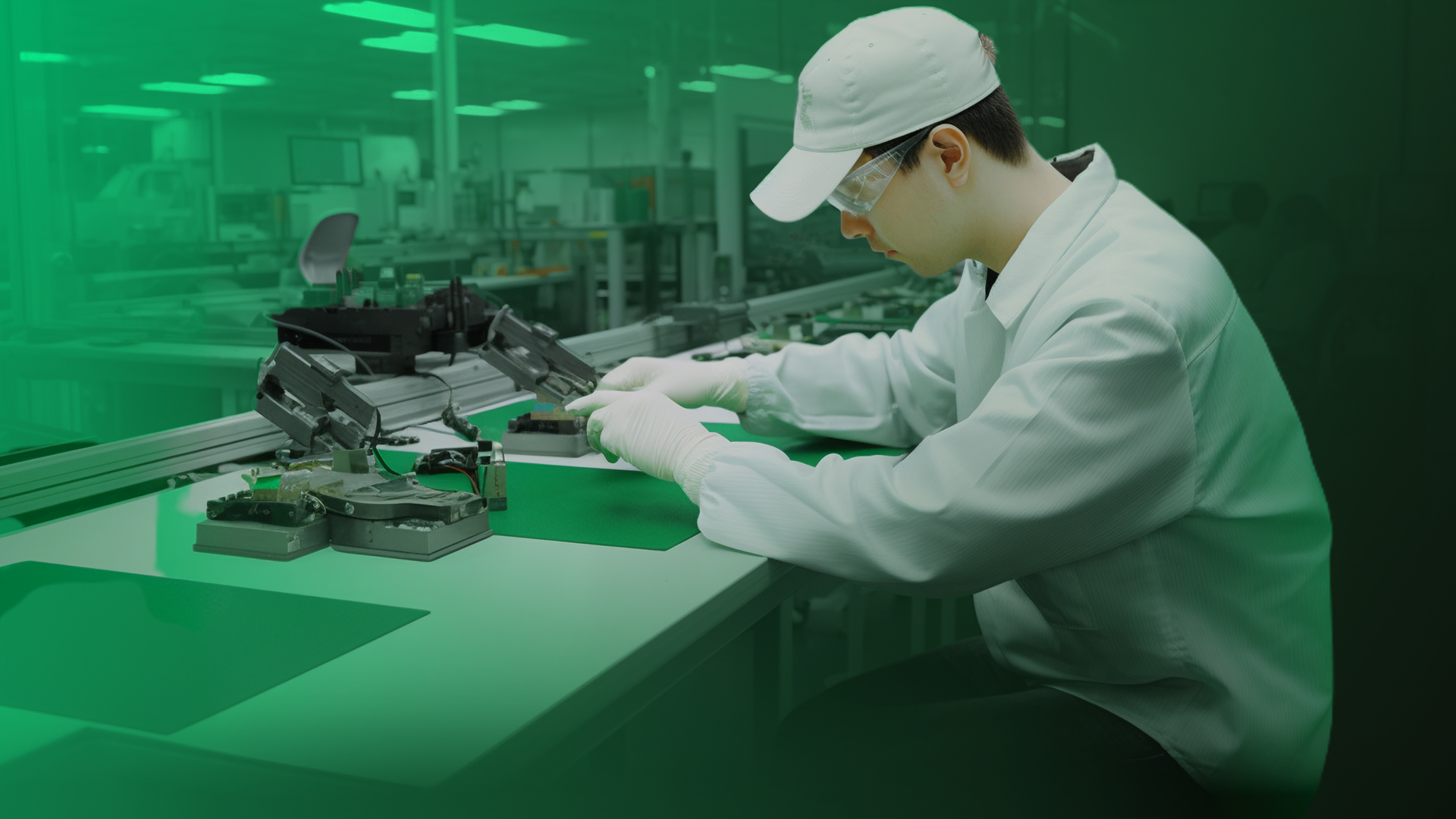
«Главный тренд — повышение плотности компонентов»: как устроено производство печатных плат и какие перемены ожидаются в индустрии
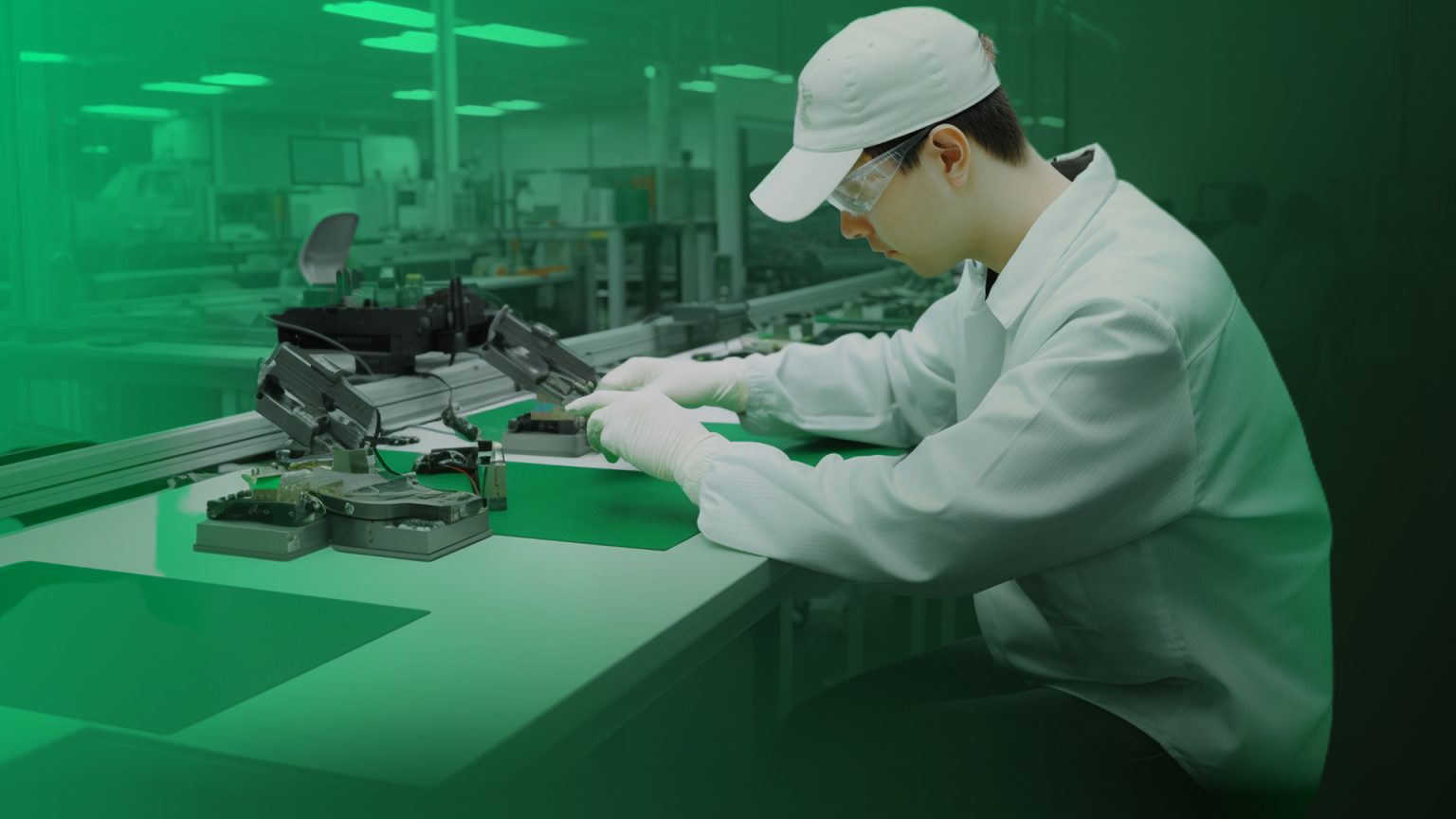
с помощью нейросети
Технолог — одна из самых ответственных должностей на любом производстве. От занимающего эту позицию специалиста зависит, насколько эффективно отлажена линейка оборудования, как точно соблюдаются алгоритмы действий и какого качества продукт поступит на рынок. Технолог на заводе по производству печатных плат должен в равной степени разбираться в химии, физике, сложной аппаратуре и психологии людей, имеющих к ней доступ. Обучиться этому в одном институте невозможно, отмечает технолог компании YADRO Виктор Захарочкин — и подробно объясняет почему.
- каковы основные процессы, влияющие на выход годных
- как выбирается оборудование
- какие сложности могут возникнуть и как из них выходить
Технолог на производстве — это тот человек, который досконально знает процесс, за который отвечает, и представляет все возможные допуски и отступы тех или иных параметров. Когда что-то случится — а что-то рано или поздно всегда случается, — у него есть все компетенции, чтобы исправить ситуацию.
Если говорить конкретно про технолога участка травления, то это человек, который прекрасно понимает, какие техпроцессы и химические реакции происходят на том или ином этапе. И если вдруг результат не удовлетворяет потребностям производства, его обязанность — оперативно внести корректировки. Например, изменить температуру, давление, концентрацию того или иного компонента в растворе.
В целом производству печатных плат нигде в России не учат, и всё из-за того, что рынок для специалистов крайне мал, а заводов такого профиля в стране почти нет. Помимо этого, в техпроцессе изготовления платы очень много различных направлений и операций. На такие места требуется универсальный человек, который разбирается и в химии, и в механике, и в физике, и в электронике, и в оптике. Конечно, в вузах дают базовые знания: что такое печатная плата, какой основной техпроцесс изготовления. Но дальше идет разделение на схемотехников, топологов, конструкторов. Больше в сторону разработки. У меня, например, специальность «Материаловедение и твердотельная электроника». Я учился растить кремний, то есть технологиям получения кристаллов. В принципе, эти процессы схожи с технологиями составления печатных плат. Основное отличие — это размеры. Кремниевая пластина — это круг диаметром 200−300 мм, размеры чипов и топологии — это нанометры и микроны.
Там был больше подход с инженерной точки зрения — из серии «какие компоненты нужно применить, чтобы схема заработала, и как ее развести, чтобы она не сломалась в процессе эксплуатации». У нас обучают больше с технологической стороны. То, что я изучал в Уэльсе, называется advanced electronics. Мы проходили курс лекций и делали лабораторные работы по испытанию тех или иных компонентов и самой печатной платы, естественно.
Достаточно сказать, что технологический процесс состоит более чем из 50 операций. В целом их можно разделить на 12−13 участков. Центральный и самый интересный — фотолитография. Это участок, на котором мы на медную поверхность будущих проводников наносим светочувствительный материал, облучаем его светом. Под воздействием света материал затвердевает, полимеризуется, а там, где его нет, он остается в пластичной форме и на следующей операции смывается.
Тут интересен подход к самому процессу, методы экспонирования. Изначально это были фотошаблоны и люди вручную совмещали их относительно платы. Далее этот этап перешел на совмещение автоматическое. Здесь мы уже можем говорить про какие-то сложные структуры.
В настоящее время для этого процесса используется прямое экспонирование. Это выглядит как аналог принтера. Есть какая-то оптическая головка, которая облучает светом материал, ездит вдоль заготовки и напрямую печатает рисунок светом.
Следующий очень важный этап — это травление. Изначально этот процесс происходил так. Брали плату с фоторезистором, окунали ее в раствор и ждали, пока он не «съест» излишки меди. При этом мы не могли никак воздействовать на раствор — скажем, заставить его травить в нужном нам направлении. Но с уменьшением габаритов проводников мы обнаружили проблему бокового подтрава, т. к. травильный раствор травит не только в вертикальном направлении, но и в горизонтальном. И вместо изначальной толщины проводника в 100 микрон мы после травления получаем 80. Соответственно, нужно учитывать это и закладывать запас. Иначе проводник может банально раствориться.
После травления мы переходим к процессу совмещения слоев между собой и циклу прессования. Это тот самый момент истины, когда создаются многослойные платы, допустим десятислойка: четыре диэлектрика, на которых с двух сторон мы уже создали травлением медные дорожки, плюс две медные фольги — будущие внешние слои. Нам надо их совместить между собой.
После прессования идет процесс сверления — тоже один из интересных моментов. Тут очень важна точность сверла, позиционирование сверла относительно контактных площадок. Чем больше увод сверла, тем больше шанс, что мы просверлим со смещением и сделаем короткое замыкание. Тогда всё, что было до этого, просто уйдет в помойку.
Следующая операция — гальваника, за счет которой мы покрываем медью стенки нашего отверстия и появляется связь между слоями. То есть ток течет по проводнику непосредственно на слой, потом переходит на стенку отверстия, которое мы покрыли медью, и поднимается на следующий слой. И таким образом мы создаем связь между внешними и внутренними слоями.
Все этапы взаимосвязаны. Если мы уменьшим диаметр сверла, чтобы получить идеальное совмещение между слоями, мы можем не покрыть это гальваникой. Если мы увеличим диаметр сверла, то мы можем допустить короткие замыкания.
Метод совмещения у каждого свой. То есть технология изготовления платы одинаковая, но подход и оборудование разные.
Для того чтобы сделать серверную плату для электронного устройства, имеющего большие габариты, подходит тот процесс, который я описал. Для изготовления планшета или мобильного телефона делается два внутренних слоя как база и потом послойно наращивается каждый следующий слой. За счет этого получается более точное совмещение между слоями. Но минус этого процесса — время его исполнения. Там много циклов прессования (до пяти), много гальванических операций, каждая из которых занимает два-три часа.
Технология, которую мы применяем сейчас, наиболее производительная и максимально упрощенная — идеальна для того, чтобы делать достаточно сложные платы. То, что вы назвали, 3D-печатью — это история сэмплов. Но пока нам проще работать в плоскости. 3D-технология — очень долгий процесс. И всегда будут устройства, в которые будут нужны прямоугольные структуры, — тот же пульт, компьютер, телевизор.
Скорость и точность совмещения топологии у современных 3D-принтеров сильно страдают и подходят исключительно для изготовления сэмплов в лабораторных исследованиях.
В целом это история лазерного оборудования: вместо того чтобы сверлить, создавать отверстия лазером. Для серверов и материнских плат нынешних поколений это еще не нужно, но в дальнейшем, скорее всего, это понадобится. И это уже есть, но вопрос, опять же, в целесообразности — оборудование дорогостоящее и медленное.
Есть стандартный технологический подход к гальваническому процессу. Имеется ряд вертикальных ванн, в них завешаны аноды, катоды. Платы погружаются в эту ванну и висят там порядка часа. Так происходит процесс гальванизации.
Следующая ветка развития — так называемый VCP (vertical continuous plating) линии. Тут заготовки не поднимаются над ванной и переезжают в следующую, а проходят сквозь нее в вертикальном положении. То есть ванны построены с левой и правой стороны относительно так называемого конвейера, углами направлены непосредственно к плате. И за счет перелива раствор постоянно попадает на плату. За счет этой технологии получается более равномерное распределение меди при гальваническом процессе. И за счет этого мы выиграем на следующем этапе травления.
По сверлильному оборудованию лидерами рынка являются Posalux и Schmoll. Это Швейцария и Германия. Они имеют каждый свои плюсы и недостатки, но в целом это как «мерседес» среди «жигулей». Но китайцы уверенно догоняют, и самое главное, они более пластичные — могут доработать свое оборудование под конкретный заказ: например, изготовить точно такую же прижимную плату, как у Posalux, причем всего за месяц. Но Китай Китаю рознь. Если зайти на сайт Alibaba, то можно найти массу китайских фирм, которые производят сверлильные станки. Бюджет — от 5 тысяч долларов и до миллиона.
По оптическим установкам мировые лидеры — это Printprocess и Orbotech. Это два топовых производителя — Швейцария и Израиль. Но у Китая уже тоже масса аналогов.
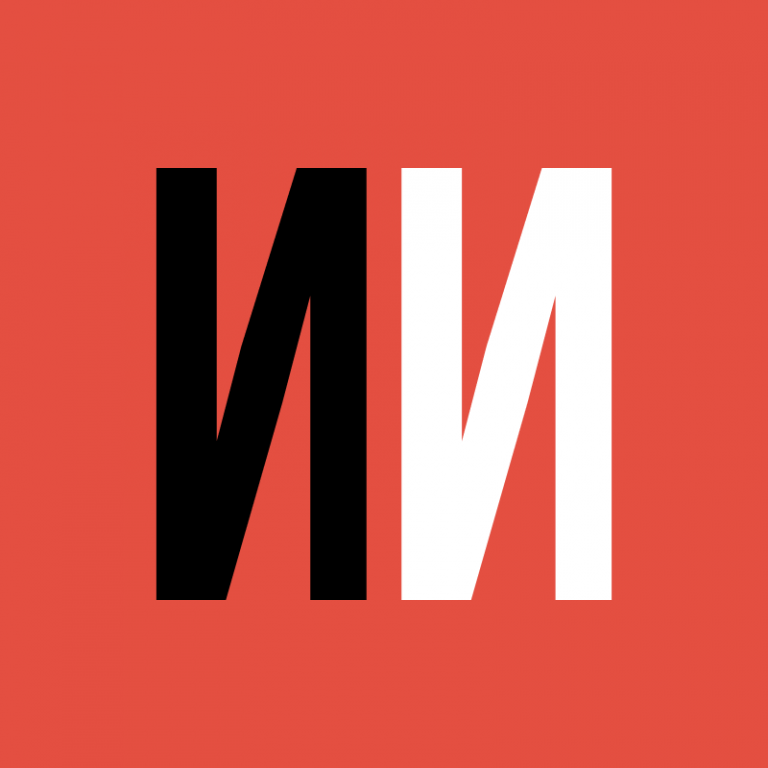
Технология производства печатных плат: теория и практика
Очень просто. Существуют ГОСТовские растворы на отечественной химии, используя которые возможно изготовить печатную плату. Но это примитивные печатные платы 3-го, максимум 4-го класса точности. Наш сервер, для сравнения, имеет 5-й и 6-й класс (а всего их семь) — то есть в два раза выше. В основном для технологических операций используется отечественная база. То есть делаем какой-то кислый раствор или щелочной и в него добавляем импортные добавки — аддитивы, которые и обеспечивают точность, надежность, воспроизводимость результатов.
Мировым лидером этих добавок является немецкая фирма Atotech. Российские заводы работают на продукции китайской компании TIANXI. Она уже успешно отработала на пяти заводах в России и нареканий по качеству я не слышу ни от одного. Аналоги есть у китайских производителей. Проблем с этим нет. Единственное, нужен более тщательный контроль.
Основной контроль на производстве печатных плат — это контроль технологий. Если его нет, мы сто процентов будем выпускать брак. Если мы контролируем технологию, то есть все возможные параметры тех или иных процессов — температуру, концентрацию химии, энергию, качество материалов, — то девяносто процентов, что мы будем выпускать качественную продукцию.
Далее, понимая, что у нас процесс работает так, как надо, и все параметры настроены, нам необходимо убедиться в том, была ли правильно сформирована подготовка к производству. Поэтому необходим визуальный контроль на каждом этапе. То есть мы изготовили слой — мы его визуально проконтролировали.
Изначально это делали люди: сидели и смотрели в микроскопы. Сейчас это АОИ (автоматическая оптическая инспекция), которая проезжает камерой по всей топологии, сравнивает ее с исходными данными. Если процесс настроен и все работает как надо, продукция будет. Если процесс не настроен, то появляются те или иные дефекты: где-то подтравы, где-то перетравы, где-то короткие замыкания
Мы закладывали в проекте порядка 75% выхода годной материнской платы. 25% — это будет брак просто потому, что это жизнь и что-то всегда случается. Как бы ни был настроен технологический процесс, что-то где-то может пойти не так.
Еще один этап проверки — электроконтроль. Летающие щупы-иголочки подбираются к каждой контактной площадке и прозванивают каждый проводничок.
После этого мы на 100% уверены, что плата годная. Но есть дополнительные испытания — чтобы быть уверенными, что эта плата проработает 5−10 лет гарантийного времени жизни. Для этого из огромной партии выпущенных нами плат отдел качества выбирает одну-две для своих разрушающих методов контроля.
Они производят испытание устойчивости к термоудару, то есть несколько раз опускают плату в ванну с расплавленным припоем, температура которого достигает 280 °C. Это абсолютно нерабочая температура для печатной платы.
Но за пять — десять циклов окунания мы увидим, что нет никаких внутри нее дефектов, потому что если есть проблемы с технологией, то она либо раскроется как мокрая книжка, либо пропадет электрический сигнал. То есть порвется медь внутри отверстия. Это один из самых эффективных экспресс-методов анализа выпускаемой продукции. Достаточно пяти циклов окунания и поднимания из горячего припоя, чтобы судить о надежности платы.
Большая часть брака идет от оператора: задумался, пересмотрел, перевернул плату, засунул в установку не той стороной. Именно для этого мы постарались максимально автоматизировать завод. Основная задача операторов — это сидеть на стуле и смотреть, что лампочка зеленая и нет никаких проблем. Если лампочка изменила свой цвет на красный или на желтый, необходимо либо предпринять самостоятельно какие-то действия, которые будут прописаны, либо обращаться к технологу, который подойдет и в ту же секунду исправит ситуацию.
Ну кто-то же должен следить за роботами. Роботы выполняют операции, там порядка 20 роботов в помещении. На них нужно хотя бы два оператора, которые за этим процессом следят.
Но степень автоматизации сейчас высокая. У нас, например, установлена система автоматической дозации растворов, причем готовых растворов. Это своего рода наш лайфхак. Обычно технологический процесс работает так. Есть линия, в ней залит раствор. Мы знаем, что в какой-то дельте параметров этого раствора он будет работать, но с каждым изменением параметра работать станет хуже. Допустим, самый примитивный раствор — это проявление фоторезиста. И мы знаем, что, чем больше фоторезиста в этом растворе, тем хуже он проявляет. И соответственно, стоит один человек на входе, другой на выходе — и запускают платы. Запустили десять плат через линию — всё хорошо. Запустили 20 плат через линию, посмотрели — хуже проявляются. Пошли скорость убавили, чтобы увеличивать время контакта растворов. Еще чуть-чуть поработали. Это человеческий контроль, который иногда иррационален, в результате которого и происходит добавочный брак. Так вот у нас всем этим занимаются роботы и раствор постоянно обновляется.
Не исключаю, что уже активно разрабатывается. Но ему тоже нужен будет технолог, который задаст ему верные параметры операций: как правильно посчитать, проанализировать, дать причинно-следственную связь и какой именно должен быть режим. Так что я автоматизации не боюсь — буду востребован. Буду приходить на работу, включать дашборд, где отображаются все необходимые мне параметры, сверять их на соответствие, что-то корректировать, если увижу отклонение, а затем ходить по производству и радоваться тому, что выпускается качественная продукция.
Тот, который сейчас существует, точно не сможет. Если он и появится в обозримом будущем у нас на производстве, то будет помощником, а не конкурентом — будет помогать мне делать автоматические анализы.
То, что печатные платы с каждым годом становятся всё сложнее, — это факт. Изначально это была односторонняя печатная плата, по сути, диэлектрик, на котором просто медный проводник — можно спокойно заменить на электрический кабель. Следующим этапом стали более сложные развитые структуры. Двухсторонние платы появились. Потом шаг вырос — появились процессоры, микропроцессоры, плата стала многослойной.
Дальнейшие перспективы печатных плат — это в первую очередь уход в меньшие размеры и встраивание пассивных элементов. То есть уже на базе печатной платы, где-то между слоем два и три, будет резистор, где-то между слоем четыре и пять — конденсатор. И тем самым мы уменьшим количество элементов, которые необходимо смонтировать на поверхностном монтаже.
Да, есть свои вызовы. С переходом на более высокие частоты уже не подходят стандартные материалы. Необходимо подбирать определенные диэлектрические параметры. Если раньше мы делали примитивную плату и она была универсальна, то теперь под каждую новую версию материнской платы необходимо детально прорабатывать, какой именно материал какой именно толщины.
С уменьшением процессоров и подложек под ними, с миниатюризацией мы как раз переходим в новую эру. Раньше достаточно было сверлить диаметры 0,5−0,6 мм — и проблем не было. Уже сейчас мы сверлим диаметры 0,2 мм, и это считается нормальной рабочей процедурой. Следующий этап — это переход на лазерные технологии, сверление отверстий 100−150 микрон. Это новый виток развития, до которого нам осталось совсем недолго.
Сейчас, если вы компьютер разбирали, видели процессор, то это металлическая коробочка, корпус, а в нем — чип на текстолитовой подложке. Эта подложка, по сути, та же многослойная печатная плата, которая разводит выводы кристалла, чтобы ее можно было удобно и комфортно намонтировать на ту плату, которую мы изготавливаем. Избавление от этой подложки — следующий прорыв в индустрии.