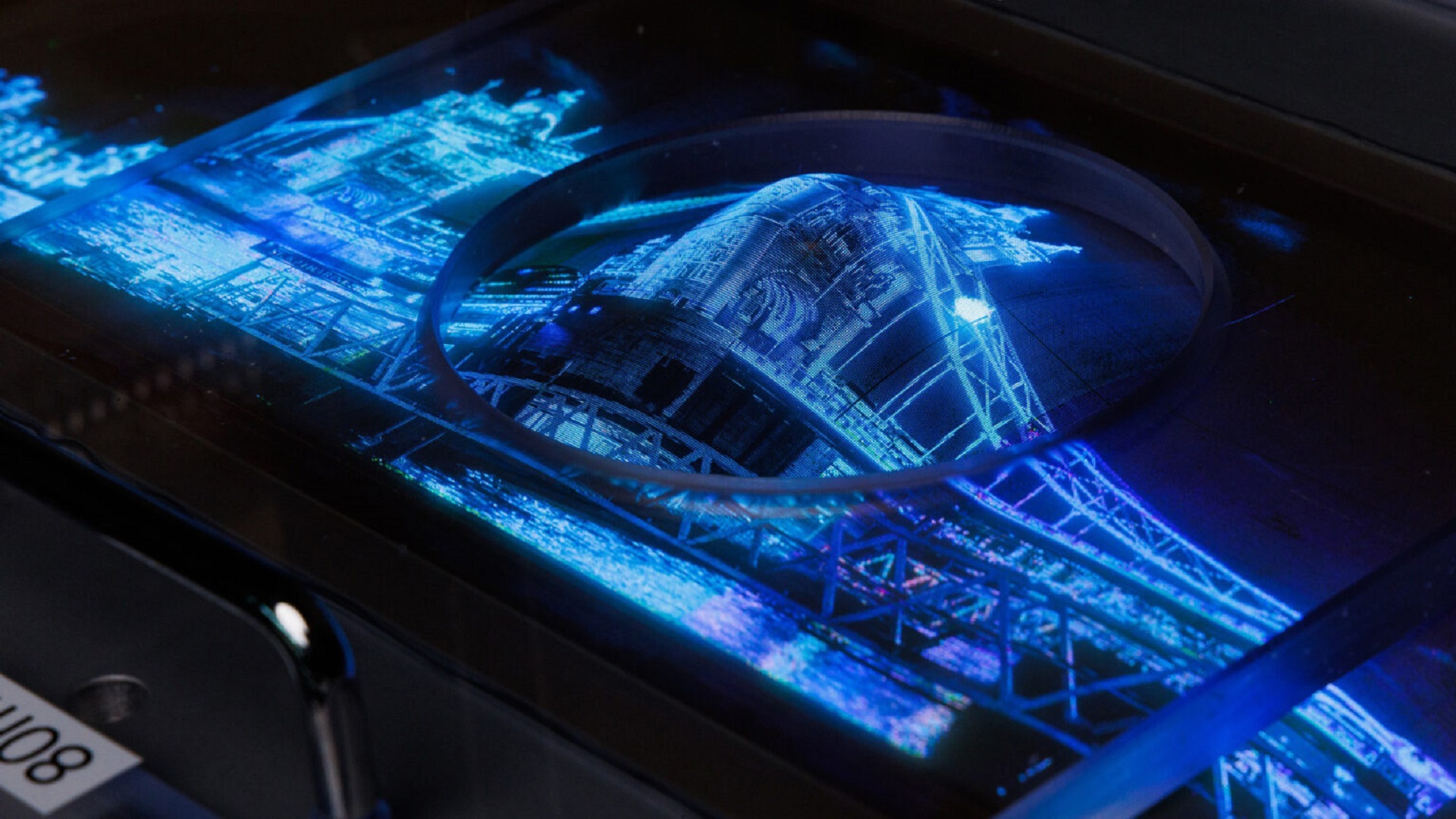
Гнут свою линию: что происходит с технологиями гибких дисплеев и как это меняет культуру пользования гаджетами
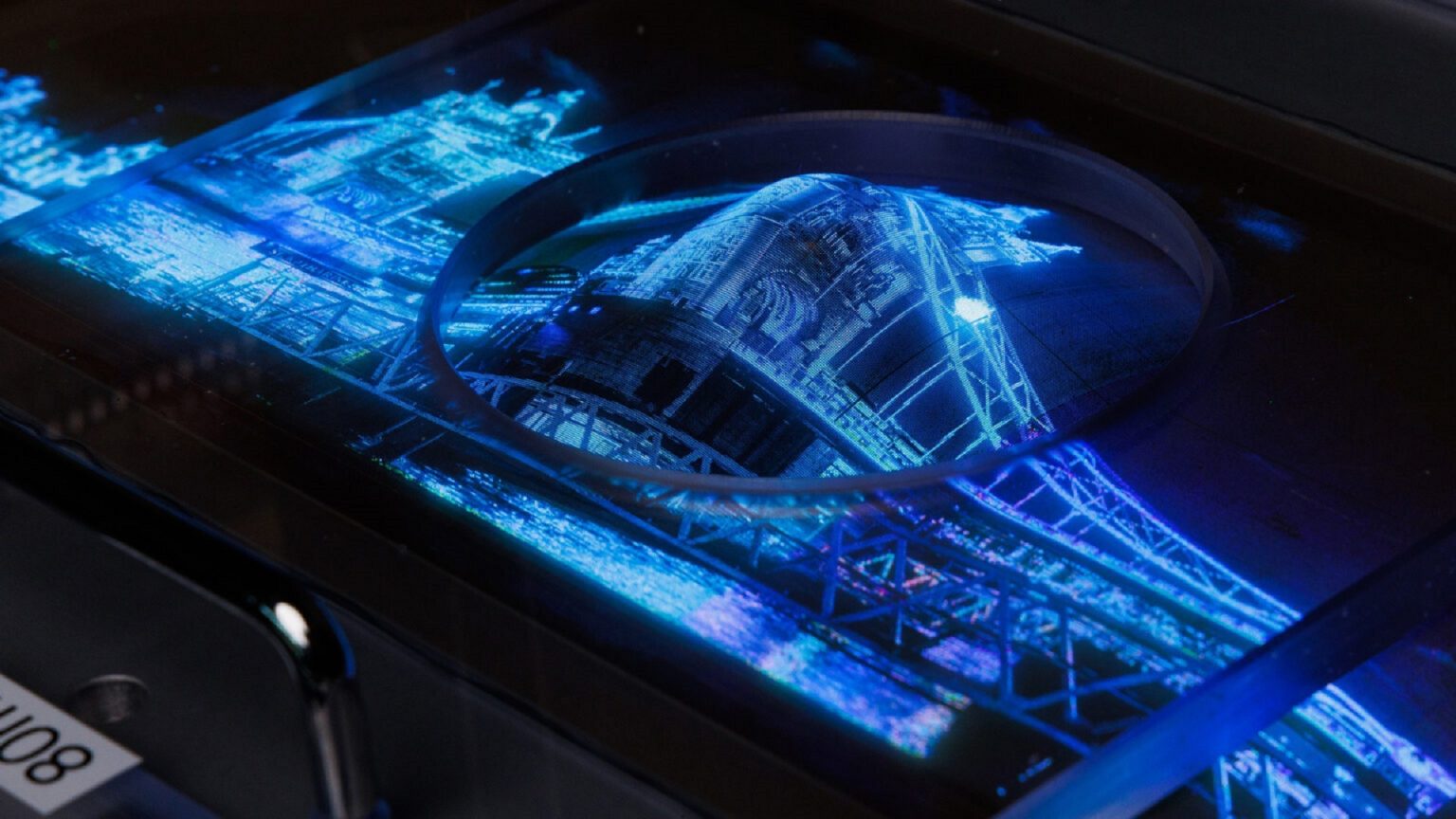
Грани возможного в использовании гаджетов размываются. Южнокорейские инженеры уже создают экраны с 50-процентным растяжением, а калифорнийские исследователи совершенствуют квантовые точки для улучшения цветопередачи эластичных дисплеев. Гибкие и тонкие, они становятся частью одежды, медицинских устройств и автомобильных интерфейсов, формируя новые стандарты взаимодействия человека с техникой. На что можно посмотреть уже сегодня и что нам покажет индустрия завтра — в этом обзоре.
Трудно представить, но гибкие дисплеи — ровесники первых карманных калькуляторов и громоздких телевизоров с цветными «ламповыми» кинескопами. В 1974 году, когда большинство людей еще удивлялись электрическим кофеваркам и барабанным стиральным машинам, инженер Xerox Ник Шеридон создал первый гибкий экран — электронную бумагу Gyricon. Она представляла собой силиконовый лист с миллионами микроскопических двухцветных шариков из пластика, плавающих в масляной среде. Под действием электрического поля шарики поворачивались, формируя черно-белое изображение. Такой экран можно было сгибать, и для сохранения картинки ему не требовалось электропитание.
Однако новацией на масс-маркете Gyricon так и не стал. Медленное обновление картинки и слабый контраст, а также пробелы в смежных сферах микроэлектроники, не дали идеи выйти за пределы лабораторий. Но она не была забыта, и в 1997 году компания E Ink сделала следующий шаг, заменив шарики на микрокапсулы с черными и белыми пигментами в прозрачной жидкости. Повысилась четкость изображения и ускорилось его обновление — началась эпоха электронных ридеров.
Полимеры нового тысячелетия
Устройства для чтения быстро завоевали рынок, но наиболее прорывное свойство их экранов — не выходить из строя при изгибе — продолжало оставаться в тени из-за неподходящих для этого подложек. Прорыв произошел уже в «нулевых», когда инженеры научились создавать гибкие полимерные подложки вместо стеклянных. Тонкопленочные транзисторы (TFT) нового поколения позволили экранам сохранять при изгибе не только структуру, но и качество изображения, а OLED-технология на основе органических светодиодов стала знаковым коммерчески успешным решением — не требовала подсветки, обеспечивала глубокий черный цвет и отлично работала на эластичных поверхностях.
Казалось, что эра гибких дисплеев уже не за горами, но оставалась нерешенной еще одна важная проблема — на что заменить оксид индия-олова (ITO), который был стандартным материалом для прозрачных электродов в дисплеях благодаря своей высокой проводимости и оптической прозрачности, но был очень хрупким и крайне дорогим.
В поисках альтернатив инженеры начали экспериментировать с серебряными нанопроволоками, углеродными нанотрубками и проводящими полимерами.
Научные изыскания в этой области продолжаются до сих пор, и уже принесли свои плоды. Ряд ярких разработок, основанных на применении новых материалов, были продемонстрированы на крупнейшей выставке потребительской электроники CES, прошедшей в январе 2025 года в Лас-Вегасе. Некоторые из них мы еще отметим позже, но пока ненадолго отправимся в Сеул, где сейчас рождаются многие инновации в сфере визуализации.
Тонким слоем
В Сеуле над внедрением новых материалов в производство дисплеев работает группа ученых под руководством профессора Сумина Кана. Научную ставку они сделали на графен — одноатомный слой углерода, за исследование которого выходцы из России Андрей Гейм и Константин Новоселов в 2010 году получили Нобелевскую премию.
Пятнадцать лет спустя ученые в Южной Кореи разработали технологию GLLO (Graphene Laser Lift-Off), использующую графен как промежуточный слой между гибким полиимидом и стеклом.
GLLO позволяет создавать полиимидные пленки толщиной 2,9 мкм, что в разы тоньше человеческого волоса. Традиционные методы при такой толщине приводили бы к деформации материала, но GLLO справляется не только с этим. Она предоставляет возможность повторного использования стеклянных подложек, существенно снижая производственные затраты.
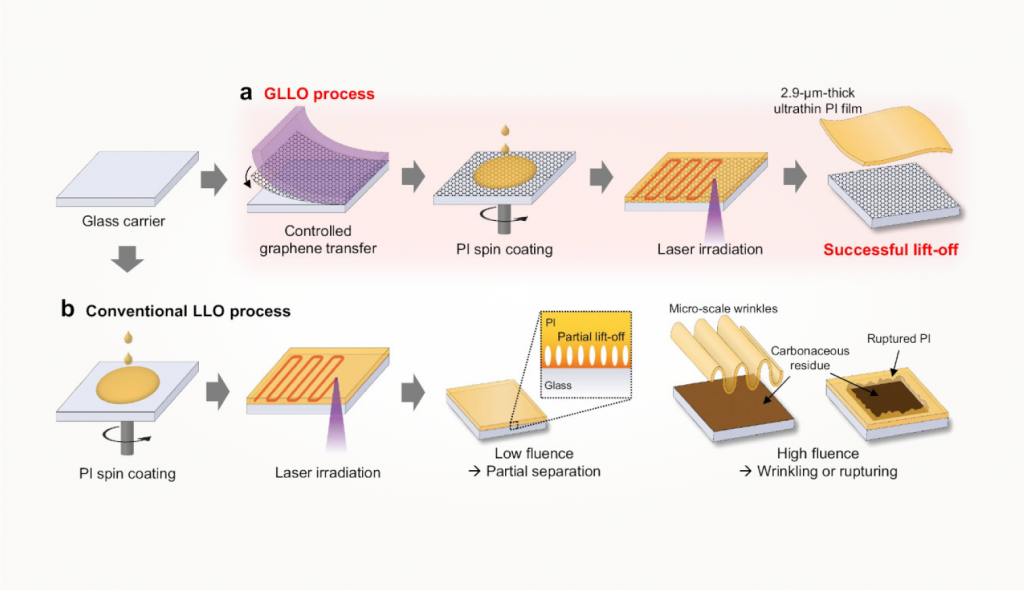
б) традиционный метод лазерного отделения (LLO).
Источник
Растянулись как следует
Пока графен помогает обходить проблему хрупких подложек, инженеры LG Display решают не менее амбициозную задачу. В конце 2024 года компания представила первый в мире эластичный экран с коэффициентом растяжения 50%. За два года технология прошла впечатляющий путь — от прототипа, способного растягиваться лишь на 20%, до 12-дюймового дисплея, свободно увеличивающегося до 18 дюймов при сохранении четкости в 100 ppi.
В основе этого прорыва — также кропотливая работа с материалами. Инженеры LG применили силиконовый субстрат, родственный материалу контактных линз, разработали новый дизайн проводников и интегрировали в девайс микро-LED размером 40 микрометров. В результате их новинка выдерживает более 10 000 циклов растяжения, сохраняя качество изображения при температурных перепадах и механических нагрузках.
LG Display продемонстрировала несколько концептов использования технологии. Среди них — автомобильная панель, изменяющая форму под управлением руки, и носимый дисплей для пожарных, интегрированный в униформу и отображающий оперативную информацию в реальном времени.
Микроэлектроника на макроуровне
Упомянутые выше микро-LED заслуживают отдельного внимания, так как широко используются при создании эластичных экранов. На выставке CES 2025 сразу несколько крупных производителей электроники представили разработки в этой сфере, и здесь корейцы вновь впереди планеты всей. Так, с мощными премьерами приехала в Лас-Вегас Samsung: компания привезла с собой прозрачные дисплеи и модели с технологией TGV (Through Glass Via), позволяющей создавать сквозные электрические соединения внутри стеклянных подложек. В экранах микро-LED она используется для улучшения проводимости, уменьшения толщины экрана и повышения прозрачности. Впервые TGV MicroLED показала широкой публике на предыдущей CES, а в 2025 году презентовала уже обновленный модуль с диагональю 144 дюйма и соотношением сторон 21:9.
Не намного отстает от Южной Кореи Китай. Hisense также удивила гостей CES, представив свой первый потребительский микро-LED — телевизор 136MX с диагональю 136 дюймов. Модель оснащена более чем 24,88 миллионами микроскопических светодиодов.
Тайваньская компания AUO и разработчик из Шэньчжэня Tianma объявили о запуске новых производственных линий, обещая сделать микро-LED доступными для массового потребителя.
Квант, и точка
За последнюю пятилетку индустрия совершила еще один большой прорыв — создала растягивающиеся светодиоды на квантовых точках. Это решение оригинально обходит главное ограничение OLED: сравнительно скромные показатели яркости и цветового охвата. QLED-панели с квантовыми точками демонстрируют более насыщенные цвета при меньшем энергопотреблении.
Однако долгое время квантовые точки оставались уделом жестких панелей — в гибких дисплеях они теряли эффективность из-за механических деформаций. Решение нашли исследователи из Калифорнийского университета, которые вместе с коллегами из Лос-Аламосской национальной лаборатории разработали функциональные электронные компоненты на основе квантовых точек селенида меди и индия (CuInSe₂).
Комбинация квантовых точек и гибких материалов объединяет лучшее из двух миров: QLED-технология избавляет от выгорания, присущего OLED, а эластичная основа делает экраны устойчивыми к изгибам.
Графские кристаллы
В другом технологическом лагере исследователи из Мичиганского и Кембриджского университетов делают ставку на перовскиты — материалы с уникальной кристаллической структурой. Им удалось создать гибкие перовскитные светодиоды (PeLED), сохраняющие работоспособность при деформации. Главная сложность, как и в случае с квантовыми точками, заключалась в интеграции перовскитов в эластичные подложки. Чтобы решить проблему, ученым пришлось разработать специальные методы нанесения материала.
Samsung на CES-2025 продемонстрировал, как эти новации меняют привычные гаджеты. Технология Slidable Flex Duet простым движением рук пользователя превращает 8-дюймовый экран в 12-дюймовый, а Slidable Flex Solo растягивает дисплей с 13 до 17,3 дюйма, предвосхищая эру трансформируемых ноутбуков. Для носимой электроники корейцы разработали модель Slidable Flex Vertical с диагональю от 5,1 до 6,7 дюйма.
Сеансы самолечения
За кулисами этих впечатляющих достижений продолжается борьба с главным противником гибких экранов — деградацией материалов. Samsung, например, внедряет в свои продукты многослойные барьерные покрытия из полиимида (PI), чередуя органические и неорганические пленки для создания барьера против кислорода и влаги. Это позволяет покрытиям выдерживать до 200 000 циклов изгиба без потери функциональности.
LG применила иной подход, разработав самовосстанавливающиеся полимеры. Еще в 2013 году компания представила смартфон LG G Flex с задней крышкой, покрытой специальным материалом, способным самостоятельно устранять мелкие царапины при комнатной температуре. Молекулы этого полимера, связанные водородными связями, «залечивают» микроповреждения, значительно продлевая срок службы устройства в условиях повседневного использования.
После презентации LG G Flex 2 в 2015 году, который также был оснащен самовосстанавливающимся покрытием задней панели, использование подобных технологий в потребительских устройствах было ограниченным. Однако исследования продолжаются. В 2017 году Motorola подала патент на экран из полимера с памятью формы, способный «заживлять» трещины при нагреве. Аналитики предсказывают появление гибких дисплеев с нанопокрытиями, заполняющими царапины при воздействии воздуха, на широком рынке до конца десятилетия.
Будущее на изломе
Несмотря на все эти достижения, на маршруте к масс-маркету у гибких дисплеев пока еще немало важных остановок. Так, даже лучшие защитные покрытия не могут полностью предотвратить износ материалов экрана, особенно в местах экстремального изгиба радиусом менее 4 мм. Помимо этого, производители часто используют несовместимые технические решения, что затрудняет унификацию и стандартизацию. И, разумеется, препятствием служит стоимость производства, которая остается высокой даже с учетом последних модернизаций. Иными словами, путь к идеальному дисплею еще не пройден, но направление движения очевидно: будущее за технологиями, которые «прогибаются» под человека, а не наоборот.