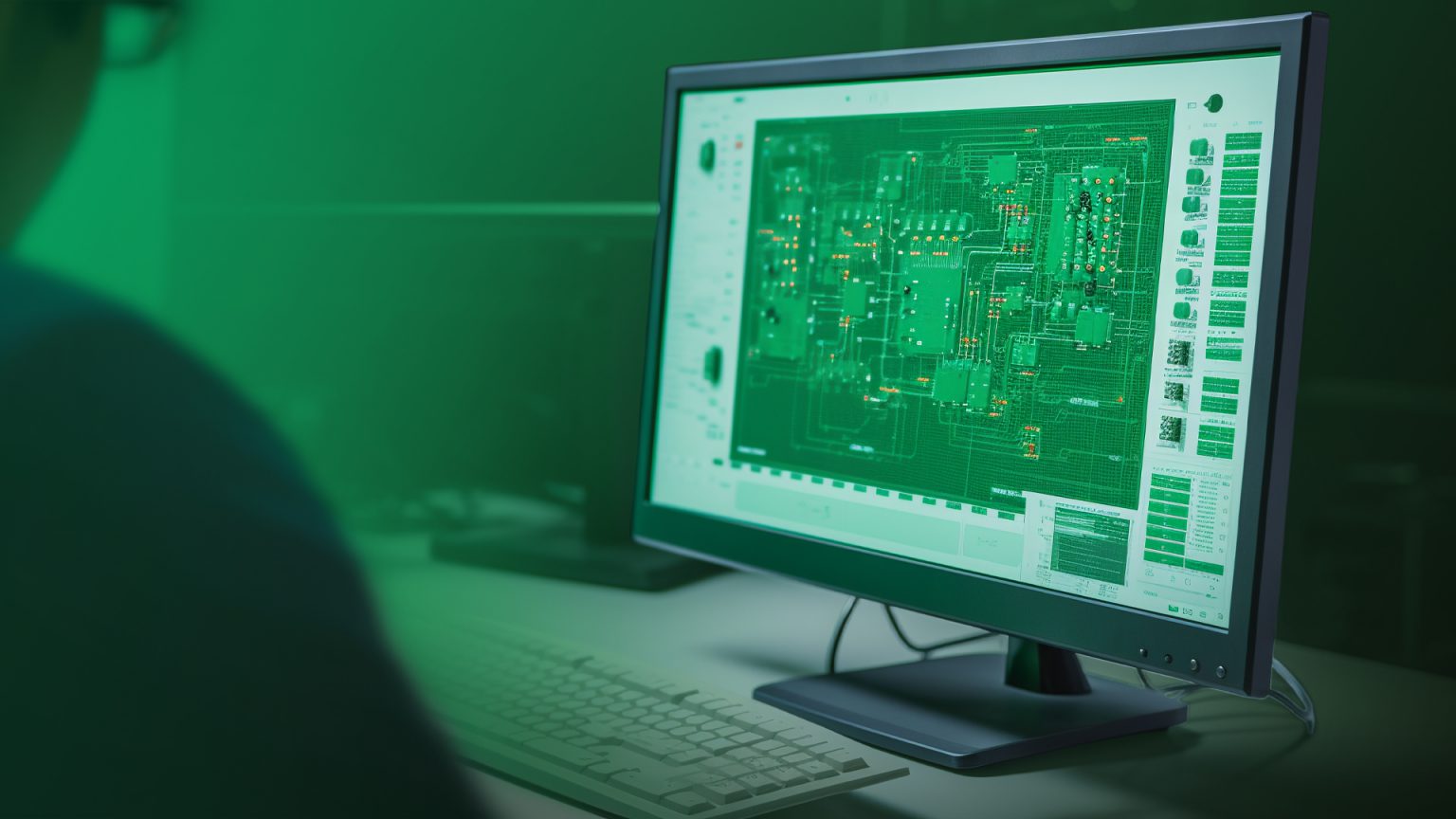
Как рождается печатная плата: подготовка проекта к запуску в производство
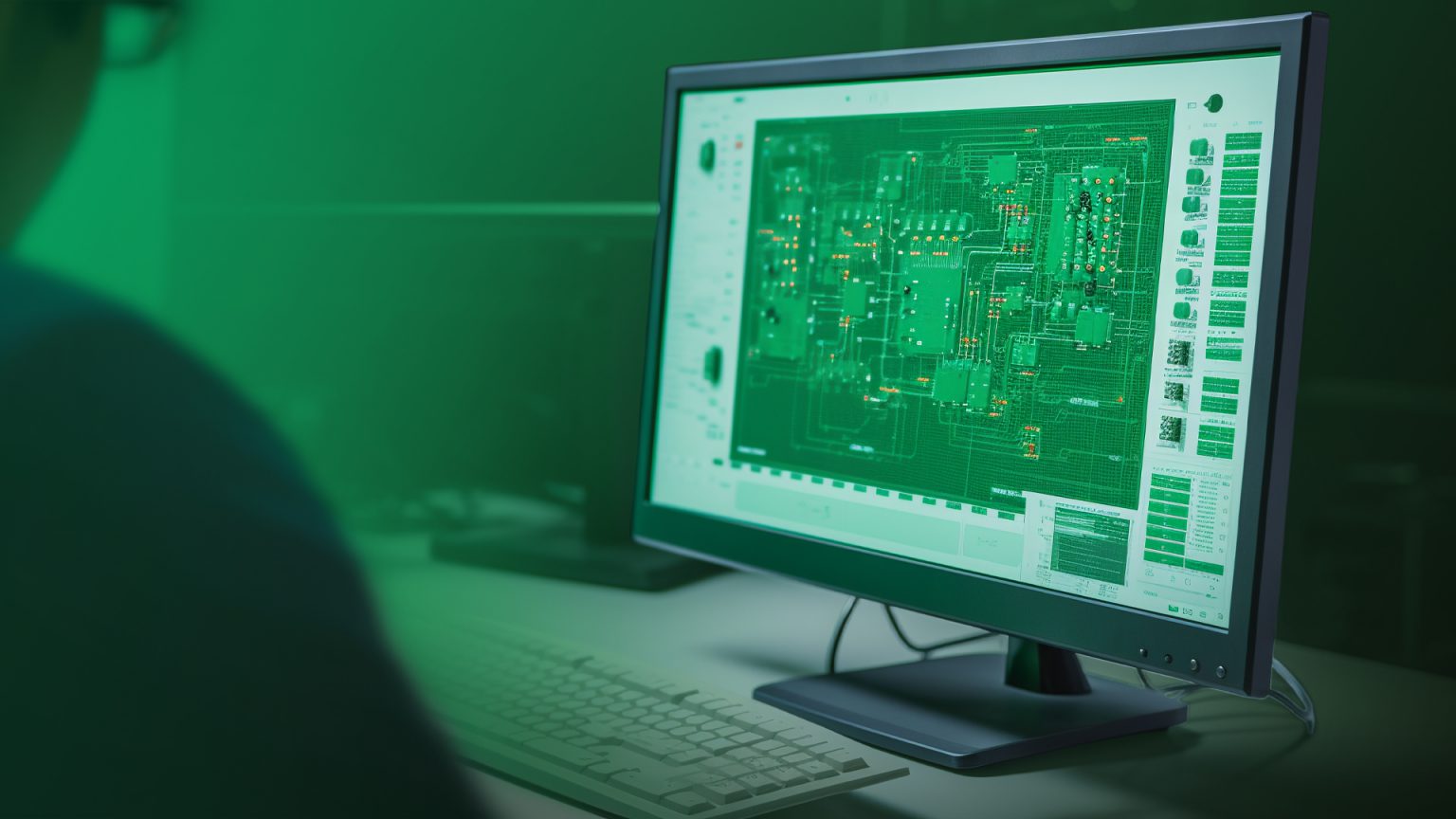
Запуск изделия в производство — важнейший этап в жизненном цикле любой фабрики. Но эта кульминация проекта — только верхушка айсберга в длительном процессе превращения абстрактного чертежа в безупречный электронный модуль.
Руководитель департамента подготовки производства по направлению печатных плат YADRO Евгений Дыбошин рассказывает, какой путь проходит печатная плата от технического замысла до физического образца, готового пойти в серию.
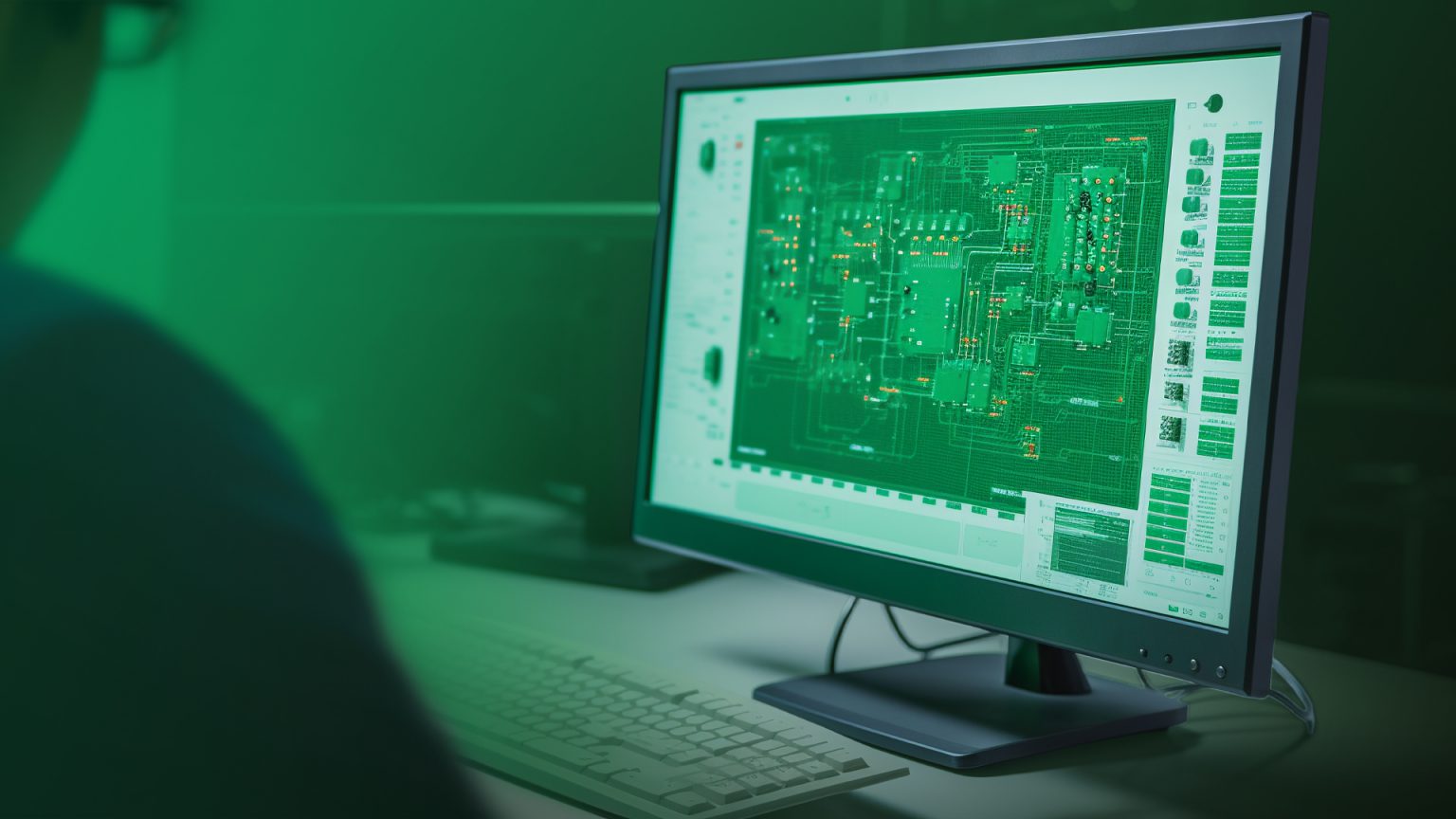
- что такое скин-эффект и зачем он нужен
- в чем различия систем Cadence Allegro и Sprint Layout
- что общего у материала для диэлектрика и шерстяного свитера
Всё начинается с заказчика, которому она нужна. Учитывая его потребности, составляется техническое предложение. В современном мире из-за сложности изделий написание ТЗ на разработку платы может занять значительное время, поэтому инженеру-схемотехнику порой проще самому «развести» плату, чем составлять объемное исчерпывающее описание. Он производит расчеты электросхем, определяет тепловые режимы работы элементов, выбирает элементную базу изделий. Когда требования к будущему изделию определены и прописаны, техническое задание и электрическую схему с просчитанными параметрами передают конструктору. Он делает компоновку, выбирает схему подключения элементов, ориентируясь на указанные габариты и другие параметры. Далее конструктор оптимизирует топологию, прогоняет проект через систему проверки целостности цепей и структуры. Разрабатывает сопроводительную документацию, такую как чертежи на плату или бланк заказа. Финальный этап — выбор производителя печатной платы.
Работа нашего отдела начинается с анализа конструкторской документации. С этого момента мы постоянно на связи с разработчиками. Прорабатываем чертежи, смотрим, сможем ли выполнить все требования, ищем компромиссы в сложных ситуациях.
Помимо анализа конструкторской документации, мы разрабатываем управляющие программы для станков с ЧПУ. Также сопровождаем производство: следим за тем, как первая плата пройдет те или иные этапы. После прессования мы должны проверить, как у нас ужались слои, и задать корректировки параметров с учетом всех усадок. Только после этого плата уходит в серию.
Но и это еще не всё. Мы проводим панелизацию под монтаж. На полях прямоугольной заготовки расставляем реперные знаки под наше оборудование, отверстия для крепления на станках, и только в конце, когда эта разметка сделана, мы вырезаем то, что напоминает готовое изделие. Если плата планируется с импедансом, то добавляем еще тест-купон для его определения.
Ну, и последнее, что мы делаем, — пишем скрипты, повышая автоматизацию процесса. Например, для импеданса мы должны создать купон на основе топологии. Скрипт берет все данные из платы и сам рисует купон без нашего участия. Но чем сложнее плата, тем критичнее присутствие человека.
Мы работаем над этим. То, что обычно делается руками, мы автоматизировали уже процентов на тридцать. И этот показатель со временем будет расти. Многое зависит от того, в каких форматах нам предоставляют файлы. Есть, например, gerber-файлы. Это послойное изображение платы со схемой сверловки. Никакой дополнительной информации они не несут. А есть файлы ODB++. Это уже непосредственно выгонка платы, которая содержит информацию о стеке и расположении компонентов. Все эти данные позволят нам сократить количество операций на этапе подготовки и повысить степень автоматизации.
С другой стороны, данные мы получаем от конструкторов и зависим от них. Эти сведения могут быть не совсем корректными. Для выявления таких неточностей мы применяем проверку отступов и правильности списка цепей (DRC). Эта DRC есть в любой CAD-системе. Но она не всё учитывает — может показать, что на определенном отрезке всё хорошо, а там на самом деле вся связь полигона «висит» на одной ниточке, которая меньше 0,1 миллиметра. Автоматизированная система может пропустить такое, а мы понимаем, что это кандидат в брак, связываемся с конструктором и указываем ему на это узкое место. При этом конструктор может быть по-своему прав: у него плата работает. Только для серийного производства такой надёжности явно недостаточно.
Всякое бывает. Сроки разработки жесткие, а проектирование платы — сложный комплексный процесс, человеческий фактор тут неизбежен. Также существуют разные CAD-системы. Есть системы с широкой функциональностью, а есть, например, Sprint Layout — самый простой. В этой системе даже инженеры без опыта могут нарисовать плату. Только какая она будет? В таком проекте никаких моделирований не будет проведено, список цепей сделают на глаз, и посадочные места окажутся не из библиотеки элементов компании, а условные. Другое дело — Cadence Allegro или Mentor Graphics, серьезные системы проектирования, в которых очень много функций. Если в инструментах такого класса и допускаются какие-то ошибки, то это, скорее всего, исключительный случай.
Да, в основном используется программное обеспечение Genesis и InCAM. Специалисты или компании, которые занимаются сложными проектами, используют один или даже несколько инструментов этого класса. Китайцы, к слову, нам присылают скриншоты из тех же Genesis и InCAM, поэтому с уверенностью можно сказать, что ими пользуется вся индустрия.
Раньше были еще Израиль, Бельгия. Например, систему InCAM разработала израильская компания Frontline. Но теперь их перекупили Штаты. CAM350 — это Downstream Technologies, тоже американцы.
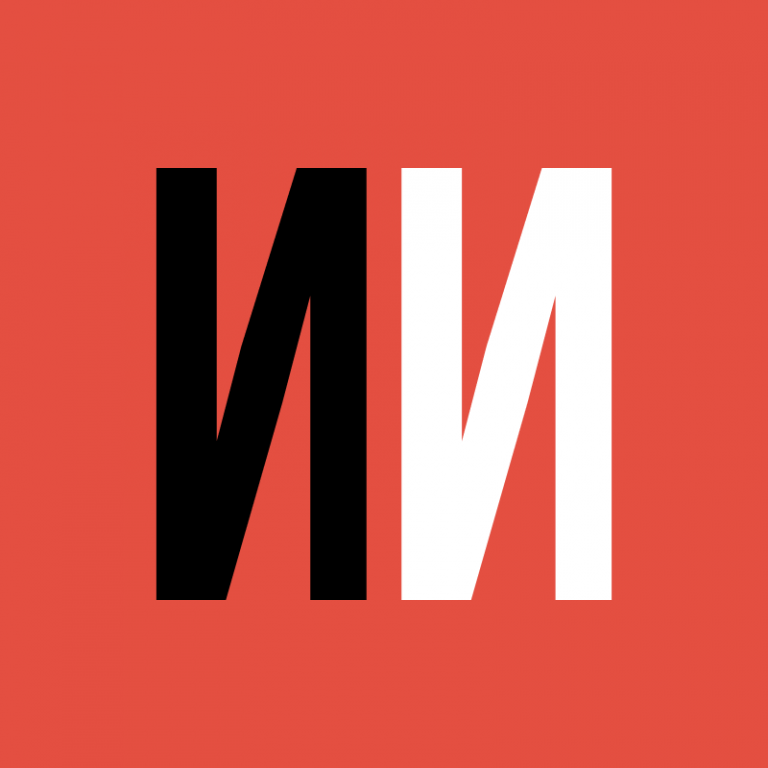
Как рождается печатная плата: подготовка проекта к запуску в производство
Напротив, каждая плата имеет свой характер. Степень ее уникальности зависит от сложности проекта и от авторского видения конструктора. Если работаешь с одними и теми же конструкторами годами, то начинаешь различать их почерк. Автоматика и программное обеспечение — только помощники.
Больше 100 тысяч.
По ГОСТу существует семь классов точности исполнения сложных печатных плат. Если у нас шестой класс уже заявлен как серийный — это очень серьезное достижение. По IPC — стандартам международной ассоциации производителей электроники — всего три класса, и мы уже в третьем. И я вам больше скажу: любой техпроцесс — он как процессор, его можно разогнать. У меня была ситуация на одном из заводов, когда еще оборудование не обновили. Что-то пошло не так с гальваникой. Мы обратились к немцам, которые строили цех, и говорим: «У нас проблема». «А вы какие платы делаете на этом оборудовании?», — спрашивают. Мы говорим: «Двенадцатислойку». В ответ: «Как двенадцатислойку! Да вы что! Эта техника не предназначена вообще для такого класса плат!»
Получается, что так. Но сейчас мы работаем уже на другом оборудовании. Надо отдать должное отрасли — она быстро меняется.
Индустрия изменится. Думаю, производители будут переходить к использованию материалов со сверхвысокочастотными свойствами. Будет усиливаться тренд на миниатюризацию. Площадь плат будет уменьшаться, и будут больше применять гибко-жесткие платы. Покрытия станут бессвинцовые, и их выбор существенно расширится.
Это физика. С повышением частоты сигнал переходит на поверхность проводника, возникает скин-эффект, то есть амплитуда электромагнитных волн увеличивается. В данном случае очень важно такое свойство поверхности, как шероховатость, а также низкий профиль фольги. Например, фольга с мелкой зернистостью — гарантия того, что потерь сигнала будет меньше. Еще эффективнее производство плат станет с улучшением тепловых параметров, так как одна из важнейших задач — максимально снизить усадку материала.
Представьте себе шерстяной свитер, который постирали в горячей воде и затем высушили. Что с ним произойдет? Скорее всего, он на вас уже не налезет. С печатными платами то же самое — когда мы травим слой или в процессе прессования проходим температуры около 260 градусов, то структура садится, как шерстяной свитер. Это вынуждает нас делать корректировки и заново печатать слои, но уже с учетом степени усадки по осям.
Почему нет? Возможно, у него будут даже идеальные параметры влагопоглощения. Сейчас, чтобы спрессовать плату, мы целый день выдерживаем стеклоткань, которая до этого хранится в холодильнике, при комнатной температуре. Такую адаптацию она должна проходить в специальном помещении с определенным классом чистоты и влажности, иначе наберет влагу, и тогда возможно расслоение при производстве платы.
Другой пример: когда мы плату изготовили, всё проверили, высушили, необходимо положить ее в вакуумный пакет и только в таком виде отправить на монтаж. В противном случае она тоже вздуется, но уже на монтаже.
Такие специалисты, как я, будут уделять меньше времени непосредственному контролю за технологическим процессом, и произойдет это по одной простой причине — степень автоматизации повысится. Вероятно, приоритетной задачей моей профессии станет как раз администрирование автоматических систем, их совершенствование и развитие. А сама подготовка платы к производству будет представлять собой единый поток, в котором мы нажатием одной кнопки будем применять к той или иной плате определенные воздействия, затем проверять, что всё хорошо, и отправлять ее в производство.