Мой путь в индустрию производства сборки печатных плат получился достаточно длинным. Первое высшее образование и опыт работы были посвящены информационным технологиям и всему, что касалось компьютерного оборудования, программного обеспечения, разработки и внедрения сложных информационных систем. Второе высшее и последующий опыт работы были уже связаны с комплексным строительством различных промышленных зданий и производств от момента проектирования до ввода в эксплуатацию. И только на следующем этапе я осуществил переход в профессию, связанную с радиоэлектроникой.
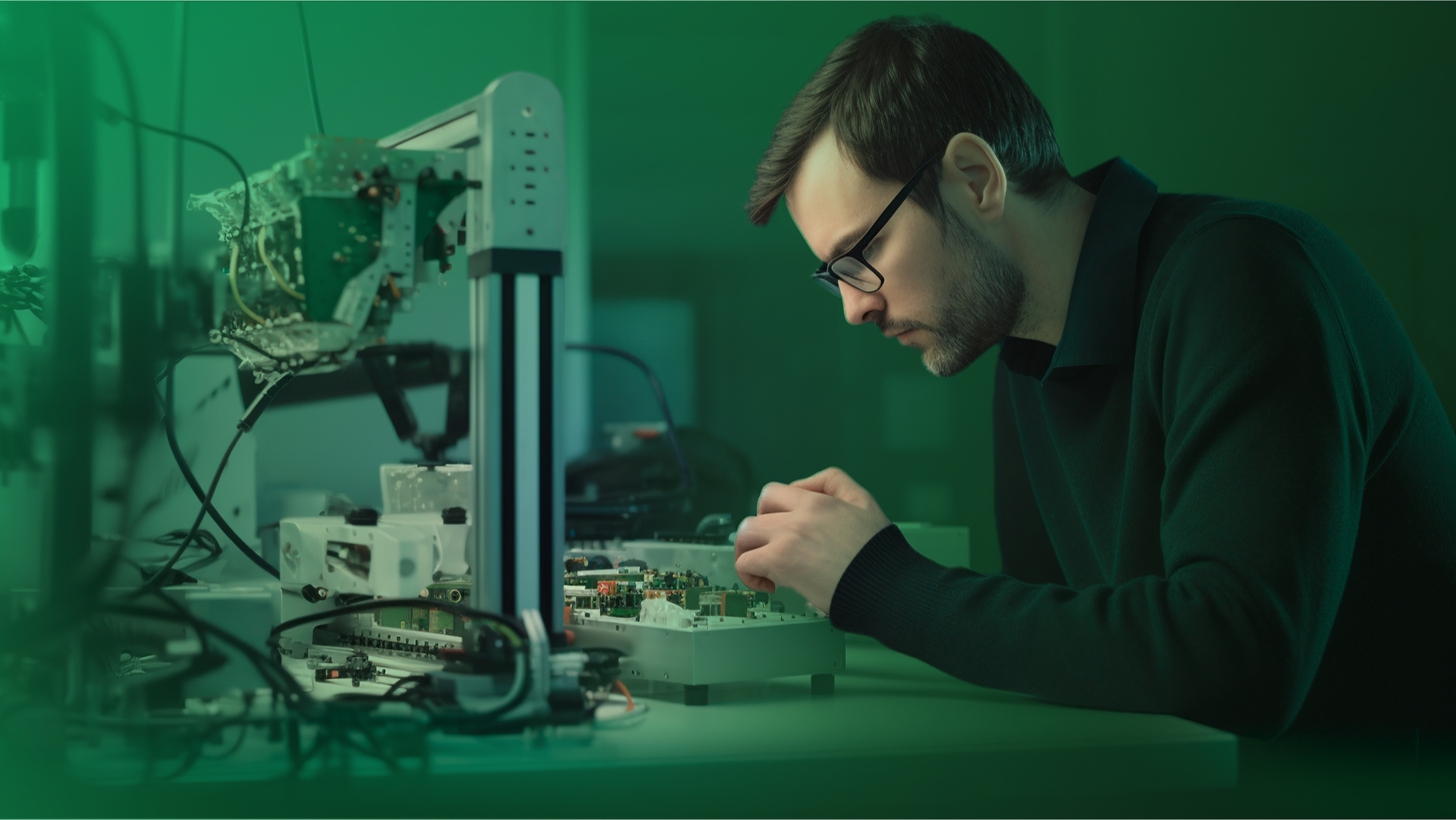
Как организовать эффективное производство на основе мирового опыта?
с помощью нейросети
Чтобы создать не просто современное производство сборки печатных плат, а производство мирового уровня, необходимо продумать множество нюансов, реализовать значительный комплекс решений. На результат влияют сотни факторов: конструкция выпускаемых изделий, применяемые технологии, логистика, используемое оборудование, квалификация персонала, подготовка помещений и инженерных коммуникаций.
Как создать эффективное производство мирового уровня и что для этого нужно, с какими сложностями можно столкнуться и что важно предусмотреть? Об этом мы спросили Сергея Морозова, заместителя генерального директора по реализации проектов компании «Остек-СМТ».
Создание современного производства — это всегда комплексный проект, в котором важно иметь опыт из разных областей и профессий. Нужно объединять людей, которые мыслят по-разному, а также формировать в единое целое технологию производства, строительство, инжиниринг и информационные технологии.
Основной критерий, по которому можно определить, что производство является эффективным производством мирового уровня, — это конкурентоспособность выпускаемой продукции на глобальном рынке.
Для этого нужно обеспечить качество и надежность выпускаемого продукта, низкое количество отказов в гарантийный период, повторяемость параметров технологических процессов.
Кроме того, цена изделий не должна превышать рыночную, а себестоимость должна быть минимизирована, но при этом нужно достигнуть эффективности вложенных в производство инвестиций. На успешность проекта также влияют технологичность изделия, продуманность производственных решений и подготовка помещений, включая вопросы строительства и потребительские свойства будущего продукта.
Эффективность всего производственного процесса напрямую зависит от эффективности оборудования, которое в нем используется. Для определения этого в мировой практике используют показатель общей эффективности оборудования OEE (Overall Equipment Effectiveness). OEE определяет процент производственного времени, которое действительно является продуктивным и позволяет понять причины неэффективности.
Измерение этого показателя обязательно для своевременного выявления и устранения потерь, проведения сравнительного анализа прогресса и повышения производительности оборудования. Так, если показатель эффективности равен 100%, это означает, что оборудование производит только качественные изделия без дефектов, с максимальной производительностью и без остановок. В реальном мире, к сожалению, такого не бывает.
Показатель эффективности оборудования OEE состоит из трех критериев:
- A — availability (доступность);
- P — performance (производительность);
- Q — quality (качество).
По результатам расчета каждого из критериев, всё, что нужно сделать для определения значения OEE, — перемножить их между собой: A х P x Q = OEE.
Перечень возможных потерь здесь достаточно ёмкий. Лучшие мировые практики достигают значения ОЕЕ 85%, многие предприятия в Европе и Азии работают на уровне ОЕЕ 70%. Эффективность российских предприятий пока редко превышает 50%.
В мире постоянно ведутся поиски повышения доступности, производительности и качества производства. Иногда изменения происходят плавно, но порой под влиянием инноваций в технологиях и технике происходит резкий скачок производительности.
В первую промышленную революцию произошла механизация ручного труда, которая кратно увеличила производительность. Стали строиться механизированные заводы и фабрики, ускорилось переселение людей из деревень в города.
Во вторую промышленную революцию произошла электрификация производства, в поточно-массовом производстве начали использовать конвейер.
Третья промышленная революция характеризовалась автоматизацией производства, совершенствованием логических контроллеров, их программированием, а также созданием промышленных роботов.
Четвертая промышленная революция (или Индустрия 4.0) происходит прямо сейчас. Кроме повышения производительности она нацелена на продуктивность, гибкость и качество. Частью этой фазы промышленных изменений является объединение таких технологий, как искусственный интеллект и робототехника. По сути, четвертая промышленная революция — это тенденция к автоматизации и обмену данными в производственных технологиях и процессах, которые включают разнородные системы и работу с большим массивом этих данных. Происходит сбор информации с датчиков и сенсоров всех точек производственного процесса, что дает производству исчерпывающий материал для анализа и принятия решений. Необходимая технология автоматизации улучшается за счет внедрения методов самооптимизации, самонастройки, самодиагностики. Искусственный интеллект и машинное обучение позволяют умным системам реагировать на различные внешние факторы, адаптируя к текущим условиям режим своей работы.
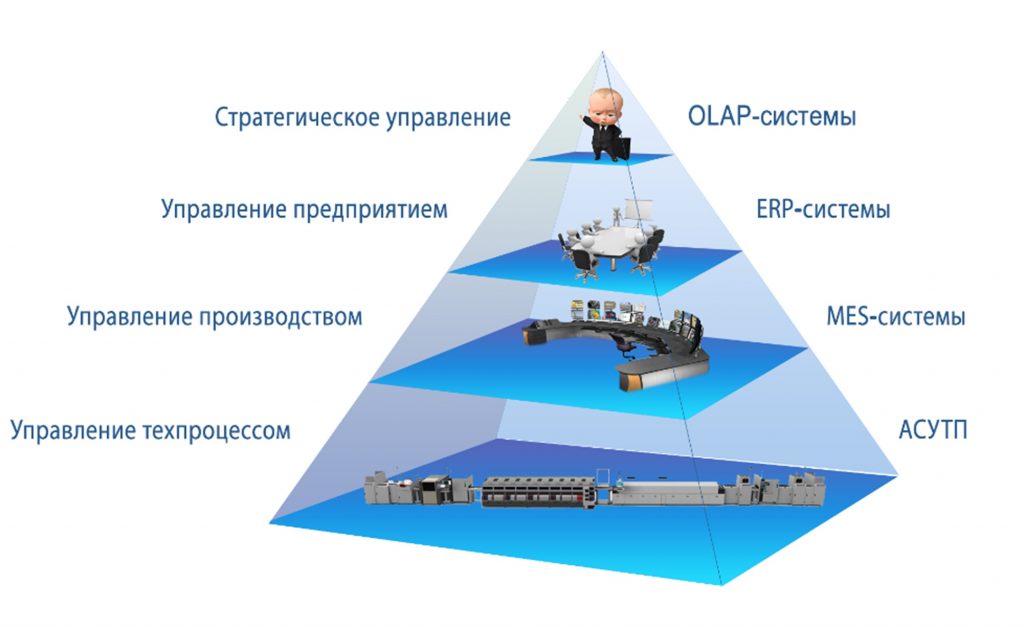
С развитием технологий Индустрии 4.0 современные предприятия в своей политике обеспечения качества переходят от поиска, устранения и выявления технологических причин возникновения дефектов к прогнозированию их возникновения и заблаговременной разработке предупреждающих мер. Конечно, предотвратить возникновение дефекта гораздо эффективнее, чем выполнять последующий его поиск и ремонт.
Индустрия 4.0 задает один из самых важных трендов мирового производства — сокращение времени вывода изделий на рынок.
Если раньше разработка нового продукта могла длиться годы, то сейчас даже в области специальной техники никого ждать не будут. Если не представить рынку новую разработку в кратчайшие сроки, конкуренты обгонят вас.
Как итог — к ключевым факторам эффективного производства мирового уровня относятся:
- минимальное время переналадки для производства разных видов изделий;
- минимальные простои на техническое обслуживание;
- максимальная производительность на единицу площади;
- минимальное энергопотребление;
- минимальные инвестиции на развитие;
- минимальное количество обслуживающего персонала;
- высокая надежность.
Улучшив эти моменты, мы можем надеяться, что наш показатель эффективности вырастет.
Любое производство в первую очередь ориентируется на продукт, ведь оно создается ради его получения. Это влияет на технологические решения, реализуемые на производстве. Процесс изготовления состоит из множества этапов, и цифровой подход к организации производства охватывает их все. Если вкратце, то основные этапы создания качественного продукта выглядят так:
- Склад
Автоматизация склада дает значительный прирост производительности и сокращение площадей хранения. Склад обменивается информацией с оборудованием технологических линий — это обеспечивает прослеживаемость от готовой платы к поставщику комплектующих.
Когда мы говорим о крупносерийных производствах, то к требованию по прослеживаемости добавляется еще и скорость работы склада. Чем меньше производство ждет обработку комплектующих, тем раньше оно выпустит изделие. В этом помогают автоматизированные станции регистрации, которые обеспечивают скоростное оприходование компонентов за счет машинного распознавания заводской маркировки.
Также интеллектуальный склад может автоматически организовывать внутреннее хранение. Система управления самостоятельно определяет наилучшее место для поддонов. Персонал только загружает и выгружает их через соответствующее окно. Все внутренние перемещения происходят без участия человека. Интересная особенность такой системы — возможность управлять дополнительными складскими площадями, например шкафами ячеистого хранения.
Автоматизированное хранение компонентов позволяет производству оперативно получить информацию о текущих остатках, хранить их в соответствии с условиями, рекомендуемыми производителем, в том числе соблюдать требования к режимам температуры и влажности, отслеживать достаточность комплектации для выполнения заказов, а также при необходимости автоматически формировать ведомости для закупки или доставки комплектующих с центрального склада. Весь учет комплектующих в автоматизированных системах хранения интегрируется с ERP-системой предприятия.
- Входной контроль
Перед началом производства компоненты — печатные платы и материалы, поступившие на склад — проходят входной контроль. Обычно этим занимается служба качества.
При получении печатных плат их сначала визуально осматривают, затем с помощью специализированных инструментов контролируют толщину и состав покрытий, проводят проверку на целостность цепей с помощью установки электрического контроля и оценивают паяемость с помощью специального тестера.
Полученные комплектующие и материалы также подвергаются визуальному контролю и проверке на соответствие параметров и отсутствие дефектов. Объем и вид контроля зависит от вида готового изделия: может быть выборочным, или если, например, это штучное изделие для космического применения, то контроль может быть близок к 100%.
- Маркировка
Цифровая трансформация производств уже перестала быть только модным трендом. Теперь это острая необходимость, предъявляющая жесткие требования к процессам сбора, хранения и использования информации. Одним из таких требований является наличие машиночитаемой маркировки на каждом элементе цифрового сборочно-монтажного производства. Маркировке подлежат комплектующие, печатные платы, оснастка, инструмент и сами станки. Любой элемент, подлежащий учету и контролю, имеет собственный уникальный код или метку.
На каждой печатной плате имеется свой код (QR-код или иной код), который наносится с помощью лазерной гравировки. Это необходимое условие для заводской системы прослеживаемости — код позволяет узнать всю историю жизни изделия на технологических этапах производства.
- Печать паяльной пастой
После маркировки все платы поступают в автомат трафаретной печати. Это критически важный этап в процессе. Принтер наносит паяльную пасту, используя подготовленный трафарет и ракель. Паяльная паста представляет собой похожую на замазку смесь порошкообразного металлического припоя и липкого флюса. Флюс служит временным клеем для удержания компонентов поверхностного монтажа на месте, а также для очистки поверхностей пайки от загрязнений и окисления. Важно, чтобы каждая площадка была покрыта правильным количеством пасты. В противном случае соединение не будет корректно установлено, когда припой расплавится в печи для оплавления.
Качественные установки трафаретной печати обеспечивают высокую повторяемостью процесса за счет контроля параметров нанесения пасты: давления ракеля, его угла, скорости перемещения, а также влажности воздуха в зоне печати, которая контролируется датчиками в составе установки.
- Контроль нанесения паяльной пасты
Качество нанесения паяльной пасты контролирует автоматическая инспекция (SPI). Если на SPI обнаружен дефект нанесения пасты, плата идет в буфер и затем на отмывку. После этого платы поступают в установщик компонентов.
- Размещение компонентов
Для монтажа компонентов на печатной плате используются специальные установщики. Каждый компонент извлекается из упаковки с помощью вакуума, захватывающей насадкой, и машина для установки помещает его в предусмотренное место на плате. Печатная плата перемещается по конвейерной ленте, в то время как электронные компоненты размещаются на ней быстрыми и точными машинами — некоторые из них могут размещать 80−100 тысяч отдельных компонентов в час. Помимо высокой производительности современные установщики компонентов обладают еще одним преимуществом — позволяют достаточно быстро выполнять переналадку (обычно в пределах получаса).
В этом процессе требуется точность, поскольку любое ошибочное размещение компонента может стать дорогостоящим и отнять много времени на ремонт.
- Пайка оплавлением
После размещения компонентов печатная плата направляется по конвейеру в печь для пайки оплавлением в соответствии с настроенным температурным профилем. Пайка осуществляется в азотной среде, что позволяет достигать более высокого качества пайки плат с миниатюрными компонентами и высокой плотностью их расположения. Инертный газ вырабатывается азотными генераторами. Желательно предусматривать два отдельных генератора — для резервирования на случай выхода из строя одного из них.
Компоненты при пайке проходят:
- зону предварительного нагрева,
- зону стабилизации,
- зону пайки,
- зону охлаждения.
Если печатная плата двусторонняя, то этот процесс может повториться.
- Автоматическая оптическая инспекция
После пайки плата проверяется на наличие дефектов с помощью специализированной системы автоматической оптической инспекции (АОИ). Одним из главных преимуществ применения АОИ является возможность выявлять систематические ошибки. Система позволяет собирать статистику дефектов, анализировать такие данные за большой промежуток времени и на основе этого корректировать процесс сборки. В зависимости от прошедшего автоматического контроля платы сортируются. Если обнаруживаются дефекты, то плата попадает в буфер BAD, если дефектов нет — в буфер GOOD. Платы с дефектами переходят на участок ремонта.
- Отмывка
Участок отмывки на предприятии, как правило, организуется в отдельной комнате, смежной помещению, где установлена сборочная линия. Если при сборке изделий используется паста, не требующая отмывки, то платы сразу уходят на этап финальной сборки.
- Финальная сборка
Здесь платы устанавливаются в корпуса и передаются на финальное тестирование, где проверяется весь функционал продукта с помощью оператора в полуавтоматическом режиме. Затем печатается серийный номер, изделия упаковывают, и они отправляются на склад готовой продукции.
Ещё год назад процесс закупки был относительно простым и понятным. Определился с технологией, рассмотрел варианты оборудования, провел детальный анализ, поторговался по цене и срокам поставки — и можно запускать в закупку. Сейчас же с учетом политической ситуации процесс закупки оборудования, материалов и комплектующих для радиоэлектроники становится абсолютно нетривиальной задачей. Европейские поставщики больше не готовы поставлять свое оборудование, а выбор китайских производителей — это всегда большая лотерея, т. к. реальные характеристики при проверке часто не соответствуют заявленным.
Вывод здесь можно сделать один: доверять поставку только опытным, проверенным и ответственным поставщикам в России, которые смогут взять на себя все риски поставки оборудования и материалов, отвечающих требованиям по созданию производства мирового уровня.
Да, внешних ограничений хватает. Сейчас есть значительные проблемы с логистикой поставок оборудования из-за рубежа. А годом ранее были ограничения из-за пандемии. Все потенциальные риски должны быть спланированы, необходимо предусмотреть временные запасы по всем ключевым видам работ.
Общероссийский опыт показывает, что обычно создают два вида графиков: для инвесторов (заказчиков) и для исполнителей. Исполнителям часто задаются заведомо невыполнимые условия и сроки, и эти графики постоянно срываются, но в итоге всё приходит к тому, что базовый график для заказчика оказывается выполненным близко к запланированным срокам. Впрочем, как показывает практика, аналогичный подход наблюдается у многих иностранных компаний, которые тоже используют понятие внешнего и внутреннего графика.
Причина этого — небезызвестный закон Паркинсона, который гласит, что работа занимает всё отведенное на нее время. Кто-то из исполнителей стремится сразу достигнуть максимального совершенства при выполнении работы, а кто-то тянет с работой и делает всё в последний момент. В любом случае получается ситуация, когда в запланированные сроки поставленная цель не достигается. Именно по этой причине менеджмент действует на упреждение и заведомо сокращает сроки реализации.
Если говорить о реальных сроках строительства крупного производства, то примерно три месяца уходит на формирование и защиту инвестиционного проекта и полгода на проектирование, которое часто идет параллельно строительству и поставке оборудования. Примерно год занимает само строительство (с нуля) и еще примерно полгода уходит на монтаж, наладку и запуск производства. Таким образом, в лучшем случае полный цикл проекта от старта до запуска первого изделия занимает 1,5−2 года с учетом того, что часть этапов выполняется параллельно.
Есть понимание, что дальнейшее развитие по созданию производств в области сборки печатных плат будет направлено, с одной стороны, на адаптацию к новым технологиям, а с другой — на оптимизацию и повышение эффективности существующих решений. Уже сейчас проявляются следующие тренды:
- Максимальная автоматизация всей внутрицеховой логистики, когда нет необходимости вручную перемещать платы и компоненты с одного участка на другой. Так все материалы, попав на склад, в автоматическом режиме будут проходить стопроцентный контроль качества, затем с помощью конвейеров и роботов передаваться на производство, проходить все необходимые этапы сборки, наладки и проверки работоспособности и, наконец, упаковки.
- Оборудование будет создаваться максимально универсальным, скоростным и заточенным на самые разные варианты производства.
- Количество ручных операций будет сводиться к минимуму. Во всём мире прямо сейчас на производствах массово применяются роботизированные руки. И их массовое применение в России пока лишь вопрос финансовой эффективности.
- Применение BIM-технологий при создании производства.
Фактически это означает информационное моделирование здания и взаимную увязку множества различных систем. Это виртуальный аналог сооружения, который позволяет всем участниками проекта работать с ним в одном информационном пространстве. Главное преимущество применения такой технологии в том, что если кто-то (например, технолог) внесет изменение в информационную модель, то об этом сразу узнают все участники проекта. Они смогут корректно отработать и предотвратить потенциальные ошибки, что позволит сократить сроки реализации проекта и снизить затраты на строительство. - Восприятие подходов Индустрии 4.0 как обычной части производства.
Эти подходы будут такими же обыкновенными, как сейчас обязательное наличие электричества и конвейеров в массовом производстве.