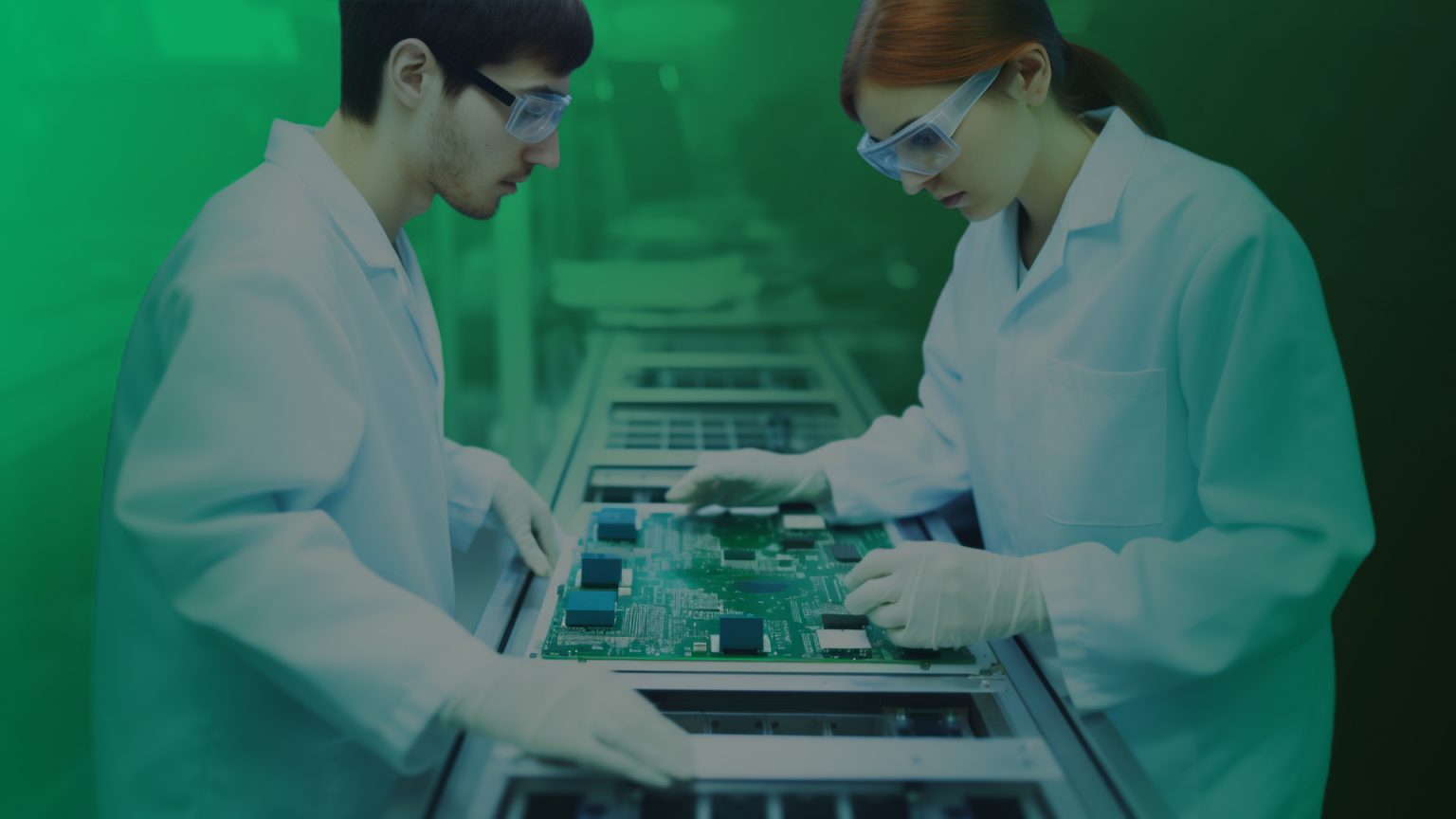
«Сборка никуда не исчезнет»: как новые технологии меняют монтажное производство печатных узлов
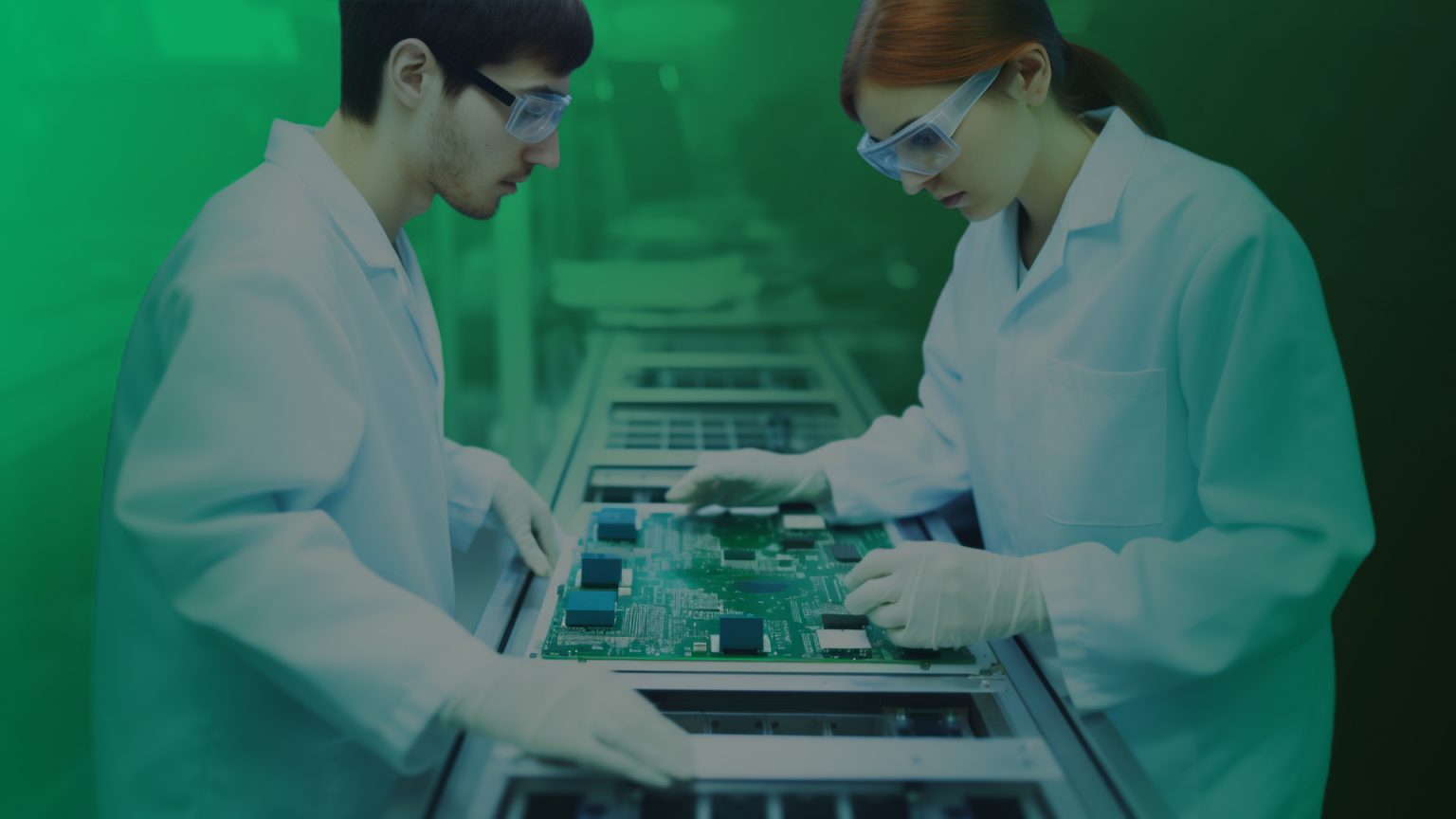
Сборочно-монтажное производство — один из наиболее консервативных этапов в процессе изготовления печатных узлов. К новым технологиям специалисты по сборке относятся с осторожным вниманием, подчеркивая, что любые нововведения должны быть продиктованы целесообразностью и необходимостью. Однако отрасль совершенствуется и производственная культура меняется вместе с ней. О том, что такое «правильные» новации, какие перемены ожидаются в традиционной сфере монтажа печатных узлов и когда руки мастера важнее автоматики, рассказывает технический директор компании «Остек-СМТ» Александр Завалко.
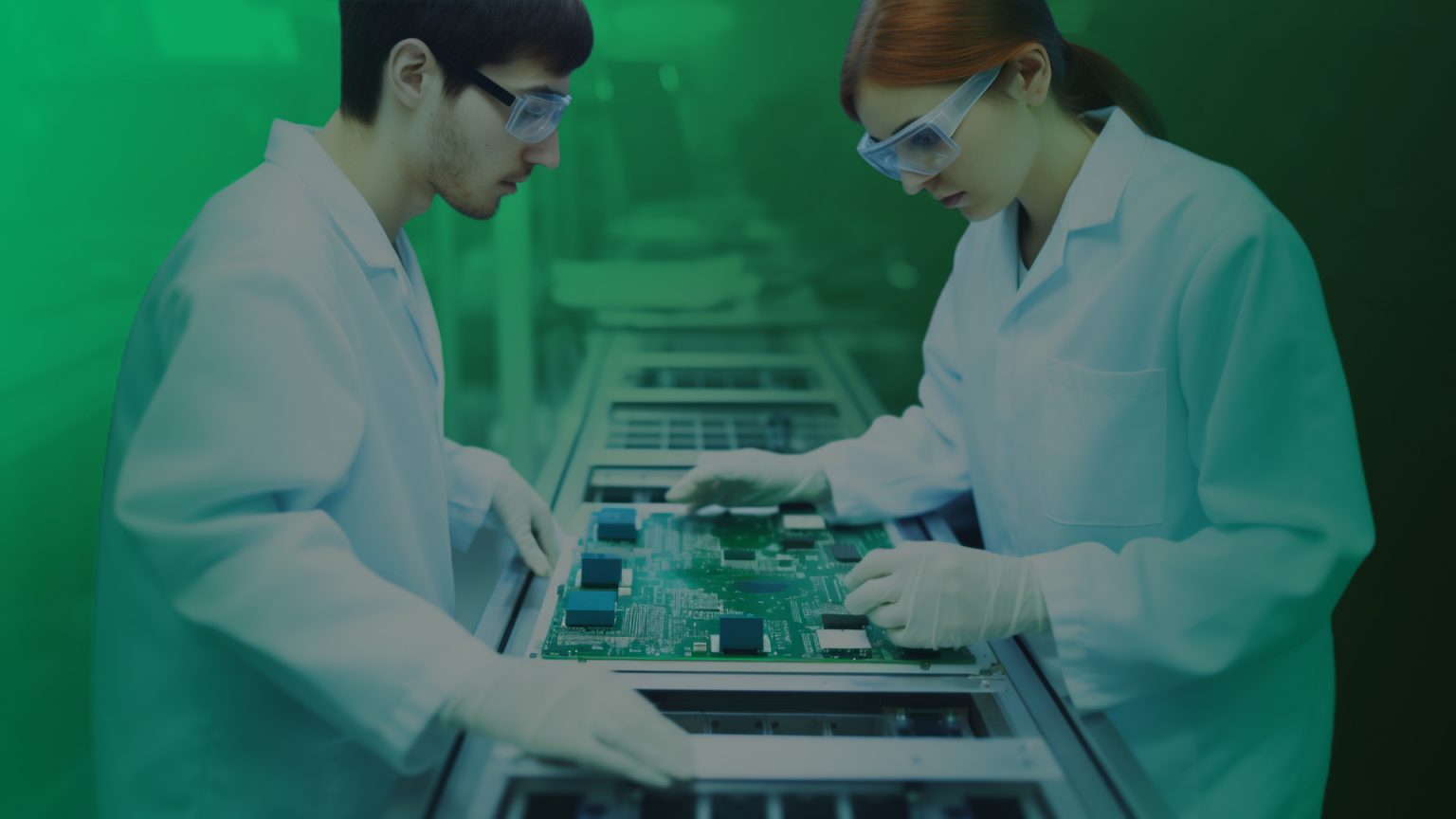
- что должен уметь уважающий себя инженер
- с чего начинается любое изобретение
- какие факторы обеспечивают готовность российского рынка к Индустрии 4.0
Я радиоинженер во втором поколении. Мои родители работали на заводе, выпускающем радиостанции. Про российское автоматическое производство электроники в 1990-х было мало информации и [с ним было связано мало] надежд. Поэтому я не пошел по стопам родных, а получил образование в области квантовой электроники и какое-то время занимался физикой и разработкой лазеров. В сборку электроники пришел позже. На тот момент поверхностный монтаж был в стране инновационной технологией. Могу вам сказать, что в начале 2000-х у нас было очень мало предприятий, которые делали его на должном уровне. Да и сейчас специалистов не хватает — поверхностному монтажу и другим автоматизированным способам сборки электроники мало учат. В этой сфере я тоже самоучка, но мне очень помогло фундаментальное физическое образование и знакомство с зарубежным опытом.
Главное — продолжать внедрять новые технологии. Как уменьшить габариты телевизоров, компьютеров без потери их функциональности? Начать их по-другому монтировать. Поверхностный монтаж позволил в свое время появиться ноутбукам. При этом, конечно, дорабатывали и сами микросхемы. Их стали делать с корпусом в виде матрицы выводов, чего раньше не было. Без поверхностного монтажа, без той технологии, которая когда-то была инновационной, а сейчас уже является стандартом, не существовало бы смартфонов или планшетов в том виде, к которому мы привыкли.
Технология действительно кажется простой. Всего три базовые операции: намазать паяльной пастой, поставить компонент, нагреть. Это можно делать даже вручную, хотя изначальная задумка была противоположной — автоматизировать под роботов. Фокус был именно на промышленную роботизацию.
Проблема в том, что на практике всё оказывается не так просто, как в теории. Робот, в отличие от человека, очень конкретен. Для него есть разница, оранжевый танталовый конденсатор или черный. Но работа технолога по инжинирингу производства в этом и заключается — перевести операции на язык робота. При правильной организации процесса робот более качественно соберет плату того же ноутбука, чем человек с паяльником. Хотя всё еще существуют предприятия, которые сопротивляются роботизации.
У меня был примечательный разговор с коллегой, отвечающим за выпуск сложной ответственной техники на другом производстве. У них в компании не хотели покупать роботов из-за опасений, что столкнутся со сложностями в ходе их установки и налаживания, не признавая, что при этом загоняют свое предприятие в технологический тупик. Ведь отказ от автоматизации сегодня приведет через десять лет к критическому отставанию.
Мне кажется, дело не в этом. Всё связано с размерами рынка. Маленький рынок стимулирует кустарное производство. Только когда артель уже не тянет, приходится строить фабрику. Однако тут есть еще другой барьер: у нас не хватает долгосрочных программ по контрактации.
Я говорю это, конечно, с известной долей обобщения. В реальности ситуация разная даже в границах одной отрасли. Есть компании, которые выстраивают систему управления так, что они готовы к Индустрии 4.0, а есть такие, которые пока не готовы.
Первые выполняют очень важную функцию — обеспечивают работой высококлассных инженеров-разработчиков, IT-специалистов, то есть тех людей, которые могут быть потенциалом для промышленности, заделом для российского экономического чуда.
Очень рад, что есть такие проекты. Но это задел на будущие десятилетия. Текущий кадровый дефицит, к сожалению, эта стратегия не устранит.
Я как «инженер-акушерка» — помогаю производству появиться на свет. У меня есть опыт как производства, так и разработки. Ко мне приходят с запросом: «Нам надо произвести такую-то продукцию в таких-то объемах». Основная задача — оценить, насколько целесообразно при данных вводных строительство собственной производственной линии. Если есть возможность этого избежать, я так прямо и говорю.
Не обязательно. Это могут быть небольшие компании, для которых крайне важно время выхода готового продукта на рынок, или организации, связанные с бытовой или промышленной электроникой и нуждающиеся в быстром прототипировании. Когда заказчики сталкиваются с трудностями на этом пути, то у них появляется идея создания своей сборочной линии. Или приходят и говорят: «Нам нужна лаборатория, чтобы успешно собирать прототипы в условиях, близких к реальному производству». Так они убивают двух зайцев: быстро прототипируют и повышают свои компетенции в сфере подготовки изделий к серийной сборке.
Основные риски — это помещение и кадры. Часто проект сворачивают на этапе поиска и подготовки площадки, потому что это оказывается либо значительно дольше расчетов, либо значительно дороже. Если этот этап пройден, то следующий большой вызов — набор квалифицированного персонала. Грамотных людей всегда не хватает.
Приведу пример из собственной практики. В 2007 году обратилась [ко мне] компания из Санкт-Петербурга, которая делала телевизионные приставки. Рынок РФ в то время активно развивался, но серьезную конкуренцию уже тогда представлял Китай. Желая побороться за больший сбыт, фирма решила основать свой завод. Нужно было спроектировать производство для сборки 3 млн цифровых приставок в год. Для успеха проекта себестоимость отечественной сборки должна была быть меньше, чем в Китае.
Был сделан расчёт, сколько надо и каких станков, как они должны быть расположены в конвейерной линии, чтобы обеспечить необходимый такт выпуска, оценка количества брака на таких объемах и так далее. Менеджмент устроила техническая проработка проекта, и они оперативно подписали контракт. Несмотря на эту оперативность, запуститься им удалось только в конце 2009 года, а выйти на проектные мощности — еще позже. Оказалось, что для старта недостаточно подключить все станки и расставить всех по местам. Очень много времени, в том числе и в моей работе, отнимает такой этап, как освоение серийного производства, когда настраиваются бизнес-процессы, обучаются люди, окончательно выстраиваются все логистические цепочки. Но в этом случае — надо отдать должное — всё закончилось хорошо: за счет своего производства компании удалось снизить цену и завоевать рынок РФ. Более того, линия, которую я им тогда просчитал, работает до сих пор.
Второй приятный момент состоит в том, что у компании получилось успешно производить заявленные миллионы приставок в год. О таких кейсах всегда приятно вспоминать.
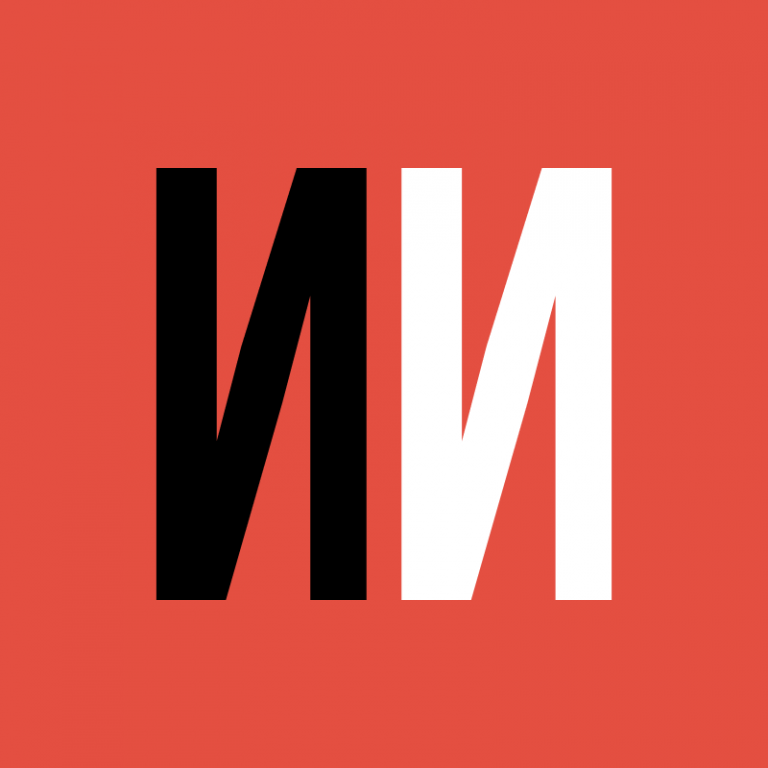
Технология сборки электронных изделий, или с чего начинается инжиниринг
Хотим мы того или нет, но цифровизация и автоматизация нас захватывает. Сегодня разработчик может использовать программу Mentor или аналогичное ПО для сквозного проектирования изделий. Если комплект конструкторской документации подготовлен правильно, то он обрабатывается в электронном виде постпроцессорами и автоматически создаются управляющие программы для станков.
С одной стороны, это, безусловно, позитивные улучшения, позволяющие экономить время. С другой — эффективность систем автоматизации тем ниже, чем выше вариативность изделий и мелкосерийность.
Российский рынок в этом плане очень специфичен. Система может классно всё просчитать в теории, но затем на практике выяснится, что прописанные в документе резисторы у нас не продаются, надо подбирать аналоги и пересчитывать.
Тут важна роль технолога, которая у нас зачастую недооценена. В России технолог на производстве электроники нередко получает меньшую зарплату, чем технолог колбасного производства. Это связано с тем, что из-за большой номенклатуры и мелких серий технологичность процесса не несет такой значимости, как в случае выпуска больших партии какого-то одного изделия.
Правильно выбранная технология — это та, которая обеспечивает нужное качество и себестоимость изделия. Если нужно собрать одно изделие, то зачастую самая правильная технология — это руки мастера, а если требуется собрать миллион, то лучшим решением будет редизайн изделия и разработка специальной оснастки, например, для замены ручной пайки на пайку волной припоя.
Любой уважающий себя инженер должен уметь обращаться с паяльником — даже в том случае, если на производстве этот паяльник не применяется, так же как хирург обязан уметь делать уколы. Безусловно, тенденции указывают на то, что ручной труд на производстве электроники постепенно будет заменяться автоматикой. Кроме того, один из трендов индустрии — переход от поэтапной сборки простых элементов к изготовлению цельных сложных деталей.
Современная инженерия стремится к тому, чтобы одна микросхема выполняла функцию десяти. А если одна микросхема выполняет функцию десяти, значит, в десять раз уменьшается количество монтажных операций. Но при этом нужно понимать, что сама необходимость сборки никуда не исчезнет, потому что только различные комбинации компонентов дают необходимую функциональность, себестоимость и качество изделий.
В основе приборостроения и электроники лежит вариативность. И это хорошо. Значит, отрасль готова к Индустрии 4.0, к производству изделий, каждое из которых не похоже на другое.
В будущем вариативность будет достигаться не за счет добавления или сокращения каких-то микросхем, а за счет программного обеспечения, которое может подключать или отключать дополнительные возможности в зависимости от того, подписаны вы на эти возможности или нет.
На российском рынке очень интересная ситуация, хотя и непростая. У нас есть элементы как европейского рынка, так и азиатского. Стареющее население, невысокие зарплаты, ограниченный внутренним сбытом спрос — все это серьезные проблемы, которые предстоит решать в ближайшие годы. Но хочу подчеркнуть, что все эти трудности важны и нужны. Кому-то может показаться, что я слишком фокусируюсь на всяких сложностях, но эти вызовы дают простор для изобретений. Есть такая теория решения изобретательских задач. Ее первый постулат — изобретение начинается с выявления противоречий. Если нет противоречий, то нет вызова на инновацию, нет запроса на прорыв. Такой застой — худший из возможных сценариев.
У меня есть сын, он школьник. Ко мне на работу пока не рвётся, но я не буду возражать, если он однажды проявит интерес к инженерному делу или естественным наукам. Хорошее фундаментальное образование позволяет выбирать разные виды деятельности. Имея образование инженера-физика, очень легко далее практиковать технические специальности в широком диапазоне.
Не сомневаюсь, что люди с фундаментальным образованием, которые умеют непрерывно учиться, будут востребованы всегда. Это та база, которая позволяет очень быстро и легко адаптироваться к любым вызовам.